Stalowa Wola wraca do pancernej czołówki
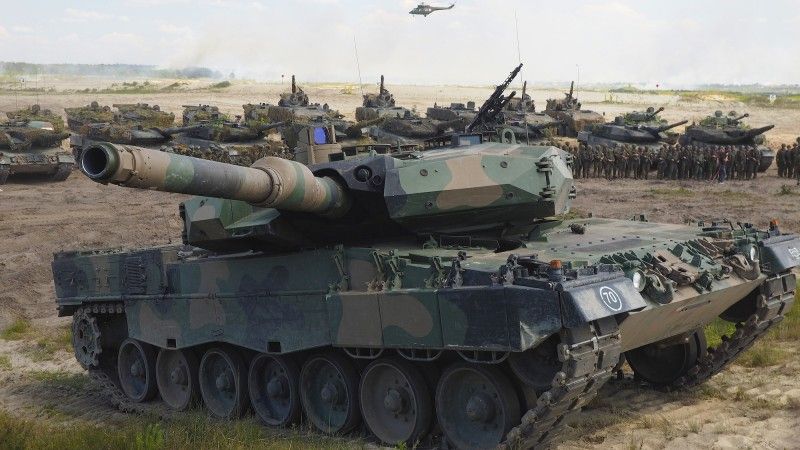
Podpisanie przez Hutę Stalowa Wola SA i Rheinmetall Waffe Munition GmbH umowy licencyjnej na produkcję części do armaty czołgowej Rh120, w tym lufy L44, stało się kolejnym potwierdzeniem, iż rozpoczęty przez stalowowolską spółkę w 1999 r. długi i pełen zakrętów powrót do czołówki europejskiej zbrojeniówki realizowany jest skutecznie i konsekwentnie. Wraz ze złożeniem podpisów przez prezesów Bartłomieja Zająca i Romana Koehne stalowowolska spółka stała się formalnym partnerem jednego z najważniejszych w świecie producentów sprzętu artyleryjskiego, którego wyroby użytkowane są przez armie kilkudziesięciu państw.
Lipiec przyniósł dwie niezmiernie ważne dla obronności naszego kraju informacje dotyczące potencjału technicznego Sił Zbrojnych RP. Pierwszą była zapowiedź MON o zamiarze zakupu w USA, w trybie procedury FMS (Foreign Military Sales), 250 czołgów Abrams w najnowszej wersji M1A2 SEPv3. Drugą – informacja o podpisaniu przez HSW SA oraz Rheinmetall Waffe Munition GmbH umowy licencyjnej, w oparciu o którą Huta Stalowa Wola pozyskała prawa do produkcji części do armaty czołgowej Rh120, w tym lufy L44. Pierwsza umowa – o ile dojdzie do jej realizacji, jako że znajduje się ona dopiero we wstępnej fazie (14 lipca szef MON poinformował, że do USA „poszedł” rozpoczynający procedurę zakupową Letter of Request LoR) – zakłada wydanie z budżetu państwa, choć, jak deklaruje rząd, spoza budżetu MON, co najmniej 23,3 mld. złotych.
Druga umowa praktycznie włącza polską spółkę w łańcuch dostawców niemieckiego koncernu, czyniąc z niej partnera technicznego i biznesowego Rheinmetall Waffe Munition GmbH, otwiera przepływ do polskiego przemysłu technologii, a przed Siłami Zbrojnymi RP – kanał nieskrępowanego niczym dostępu do tak newralgicznych elementów armaty czołgowej jak lufa. Pozwoli to, przede wszystkim, na skrócenie drogi pomiędzy MON a producentem luf. Zakłada się, że wpłynie także na obniżenie kosztów pozyskiwania tych najszybciej zużywających się części armaty, decydującej o jej skuteczności, a tym samym – o realnej wartości bojowej czołgu.
Leopardy 2 w wersjach A4 i A5 Polska pozyskała od Niemiec w trybie zakupu tych wozów nie z linii produkcyjnej, ale nabyła pojazdy używane, o różnym stopniu zużycia poszczególnych podzespołów, w tym armaty i jej lufy. Teoretyczną jej żywotność producent określa na ok. 1500 wystrzałów, i to w odniesieniu do amunicji ćwiczebnej PZ541. Jeśli stosowana jest amunicja bojowa, głównie podkalibrowa, zużycie lufy wzrasta, a jej żywotność obniża się. W pewnym momencie, za sprawą ścierania się ścianek przewodu lufy, odbywającego się w dodatku w warunkach oddziaływania wysokich ciśnień (w Rh120/L44 dochodzą one do 670 MPa) oraz wysokich temperatur produktów spalania ładunku miotającego, lufa „traci wymiar”. W największym skrócie – zwiększa się luz pomiędzy ścianką lufy a bryłą pocisku (lub jego sabotu).
Skutkiem tego jest spadek ciśnienia gazów oddziałującego na pocisk, czyli zmniejszająca się prędkość wylotowa pocisku, a tym samym jego energia kinetyczna, co skutkuje zmniejszeniem się zasięgu strzału skutecznego, celności i tym samym obniżoną przebijalnością na określonym dystansie. Zanim do tego dojdzie, lufę należy wymienić na nową, zapewniającą zachowanie wyjściowych parametrów armaty.
Czytaj też: Borsuk na Dragonie-21 [FOTO]
Dotychczas operacje wymiany zużytych luf na pełnowartościowe mogły być prowadzone wyłącznie w oparciu o zakup luf u producenta armat, co wiązało się z koniecznością nawiązywania umów uwzględniających np. wahania kursów walutowych, a także akceptację określonego okresu realizacji zamówienia przez producenta mającego zamówienia od wielu podmiotów. Teraz, po podpisaniu umowy inicjującej produkcję luf w kraju, nie będzie konieczne zamawianie ich u zagranicznego dostawcy.
Jak wiele luf armaty Rh120/L44 ponad 240 polskich Leopardów wszystkich wariantów wymagać będzie wymiany? O tym wojsko nie informuje, ale można założyć, że w relatywnie bliskiej przyszłości, do roku 2030, konieczność ta dotyczyć będzie około 100 szt. Jednak już w perspektywie co najmniej 20 lat dalszego życia około 40-letniej przecież konstrukcji (dotyczy to przynajmniej 142 wozów w wersji A4, przeznaczonych do modernizacji do wersji 2PL) z dużym prawdopodobieństwem zapotrzebowanie wojska na lufy czołgowe można oszacować na nawet 150-200 sztuk. Tempo wymiany luf zależeć będzie głównie od intensywności ćwiczeń ogniowych Leopardów, w tym – strzelań z wykorzystaniem amunicji bojowej, a także od typów tej amunicji.
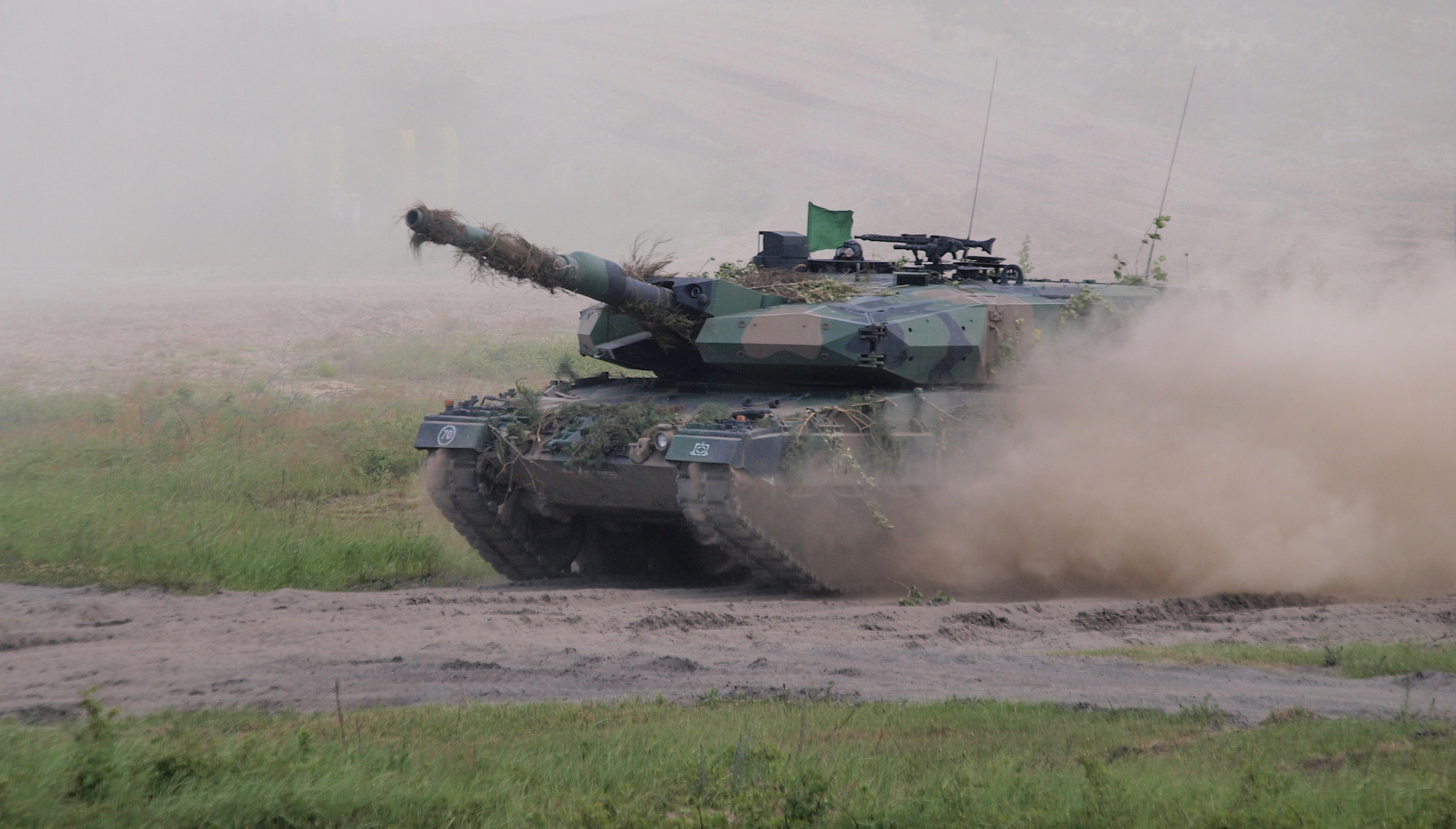
Ten nieco „wyspekulowany” wolumen produkcji luf na potrzeby polskiego wojska należy powiększyć o niemożliwą dziś do precyzyjnego określenia liczbę luf, jakich będą potrzebować inni użytkownicy czołgów Leopard 2 z armatą Rh120/L44, którzy będą lokować zamówienia u niemieckiego producenta czołgów/armat. Stanowią one znaczący odsetek wśród ponad 3 tys. dotychczas wyprodukowanych czołgów tego typu, użytkowanych w armiach blisko 20 państw Europy, Azji, Ameryki Południowej i Bliskiego Wschodu. W armatę z lufą o długości 44 kalibrów (L44) wyposażone są czołgi pochodzące z serii produkcyjnych od początku produkcji Leoparda 2 do lat 90. kiedy zmodernizowano armatę wyposażając ją w lufę o długości 55 kalibrów (L55). Ta konieczność zwiększenia możliwości armaty Rh120 w zakresie zwiększenia jej przebijalności spowodowana była pojawieniem się po drugiej stronie potencjalnego konfliktu nowych czołgów z pancerzami nowej generacji, a także z upowszechnieniem się pancerzy reaktywnych, stawiających nowe wyzwania konstruktorom amunicji przeciwpancernej. Pierwsza wersja armaty (L44) montowana była nie tylko w niemieckich Leopardach, ale także – jako wyrób licencyjny – we włoskich Ariete C oraz japońskich Typ 10 i Typ 90.
Światową karierę armacie Rh120, i to w wariancie L44, zapewniło przyjęcie jej na uzbrojenie wprowadzonego do produkcji w 1980 r. czołgu Abrams, wyprodukowanego dotychczas w liczbie ponad 10,7 tys. egz. i użytkowanego w siedmiu krajach, z tego w liczbie ponad 8,8 tys. w armii USA. Amerykanie, po pozyskaniu licencji na Rh120, zmodyfikowali i rozwinęli jej konstrukcję. Zmiany nie ograniczyły się tylko do innego systemu tłumienia energii odrzutu armaty (oporopowrotnik hydrauliczny zastąpiono mechanizmem sprężynowym) i wprowadzenia programatora amunicji. Po szeregu zmian, jako M256, wdrożona do produkcji w 1985 r. armata stała się uzbrojeniem nie tylko Abramsów.
Warto przypomnieć, że armata Rh120 została skonstruowana w połowie lat 70. ubiegłego wieku w odpowiedzi na wprowadzenie do masowej produkcji radzieckich czołgów z rodziny T-72 uzbrojonych w gładkolufową armatę 2A46 (D-81 TM) kal. 125 mm. Dawało to czołgom Układu Warszawskiego istotną przewagę nad ich odpowiednikami w armiach NATO, w których standardem uzbrojenia była gwintowana armata 105 mm. Ta z kolei była zachodnim odpowiednikiem podstawowej armaty czołgowej w Układzie Warszawskim, gwintowanej armaty D-10T, podstawowego uzbrojenia czołgów poprzedniej generacji, z rodziny T-54/T-55. Do czasu wejścia do użycia armat kolejnej generacji, m.in. o kalibrach 130-140 mm, współczesne czołgi świata zachodniego będą niejako skazane na Rh120 i jej pochodne.
Bartłomiej Zając, prezes zarządu HSW SA, mówiąc o tym, iż „produkcja luf do czołgów poszerza aktywność HSW w projektach pancernych”, dodaje: – Uzyskana licencja na produkcję luf do czołgów sprawia, że HSW SA będzie dysponować od tego momentu całym spektrum artyleryjskiej produkcji lufowej oraz zyskuje zupełnie nowe kompetencje i możliwości biznesowe w zakresie produkcji luf czołgowych. Dla naszej firmy jest to kolejny kamień milowy w budowaniu wyspecjalizowanej produkcji wojskowej na rzecz Wojsk Lądowych.
To, co nie zostało wypowiedziane wprost, wiąże się z pozyskaniem przez HSW nowych możliwości technologicznych. Te, którymi HSW SA dysponuje dziś, już i tak stawiają spółkę wśród czołowych producentów sprzętu artyleryjskiego w Europie. Teraz dokonany zostaje kolejny znaczący krok do przodu, i to postrzegany nie tylko na poziomie prestiżu firmy, ale i na polu czysto technicznym.
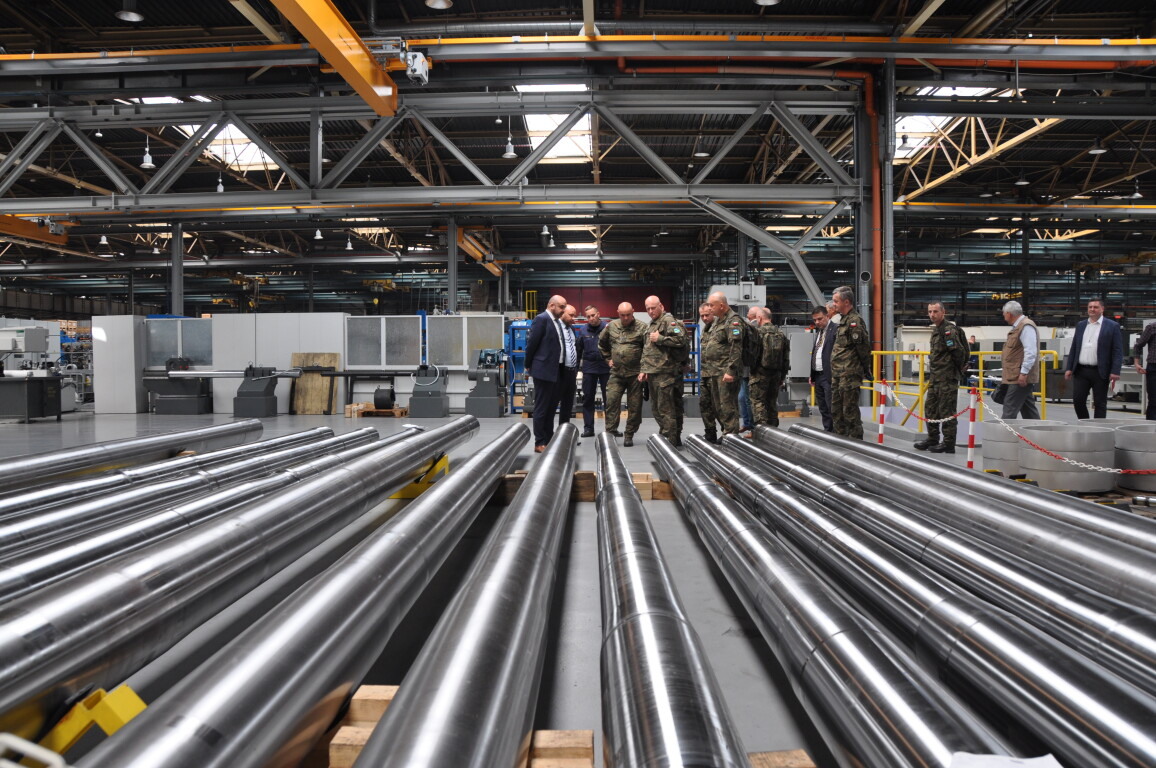
Aby uzmysłowić sobie, jak długą drogę już HSW przebyła, warto cofnąć się do roku 1999, kiedy to, dokładnie 26 lipca, podpisana została umowa na licencję systemu wieżowego brytyjskiej armatohaubicy 155 mm AS90/52. Przyjęło się stawiać tezę, iż był to „kamień węgielny” polskiego członkostwa w NATO, jako że formalnie wprowadzał do Wojska Polskiego pierwszy NATO-wski standard uzbrojenia. HSW prace koncepcyjne nad takim działem podjęła praktycznie pod koniec masowej produkcji samobieżnej, pływającej haubicy gąsienicowej 122 mm 2S1 Goździk, w latach 1994-1996.
Przyjęto dość trudne do zaakceptowania przez część ówczesnych decydentów założenie, że następca tej popularnego, używanego w kilkudziesięciu krajach Goździka (w HSW wyprodukowano ich ponad 600) będzie już dysponować działem o NATO-wskim kalibrze 155 mm, choć w armiach Układu Warszawskiego w tej grupie królował kaliber 152,4 mm. Dopiero perspektywa przyjęcia Polski do NATO urealniła te plany. Po skomplikowanych zabiegach wybrano zachodniego partnera, jakim była firma Royal Ordinance, należąca do British Aerospace. Pierwotne założenia zasad współpracy z Brytyjczykami przewidywały, iż pancerny ośrodek gliwicki dostarczy podwozie gąsienicowe dla nowej armatohaubicy (ostatecznie postawiono na licencyjne podwozie K9, produkowane w HSW). Od początku zakładano natomiast że HSW produkować będzie system wieżowy i integrować całość, zaś od Brytyjczyków pochodzić będzie kompletne działo.
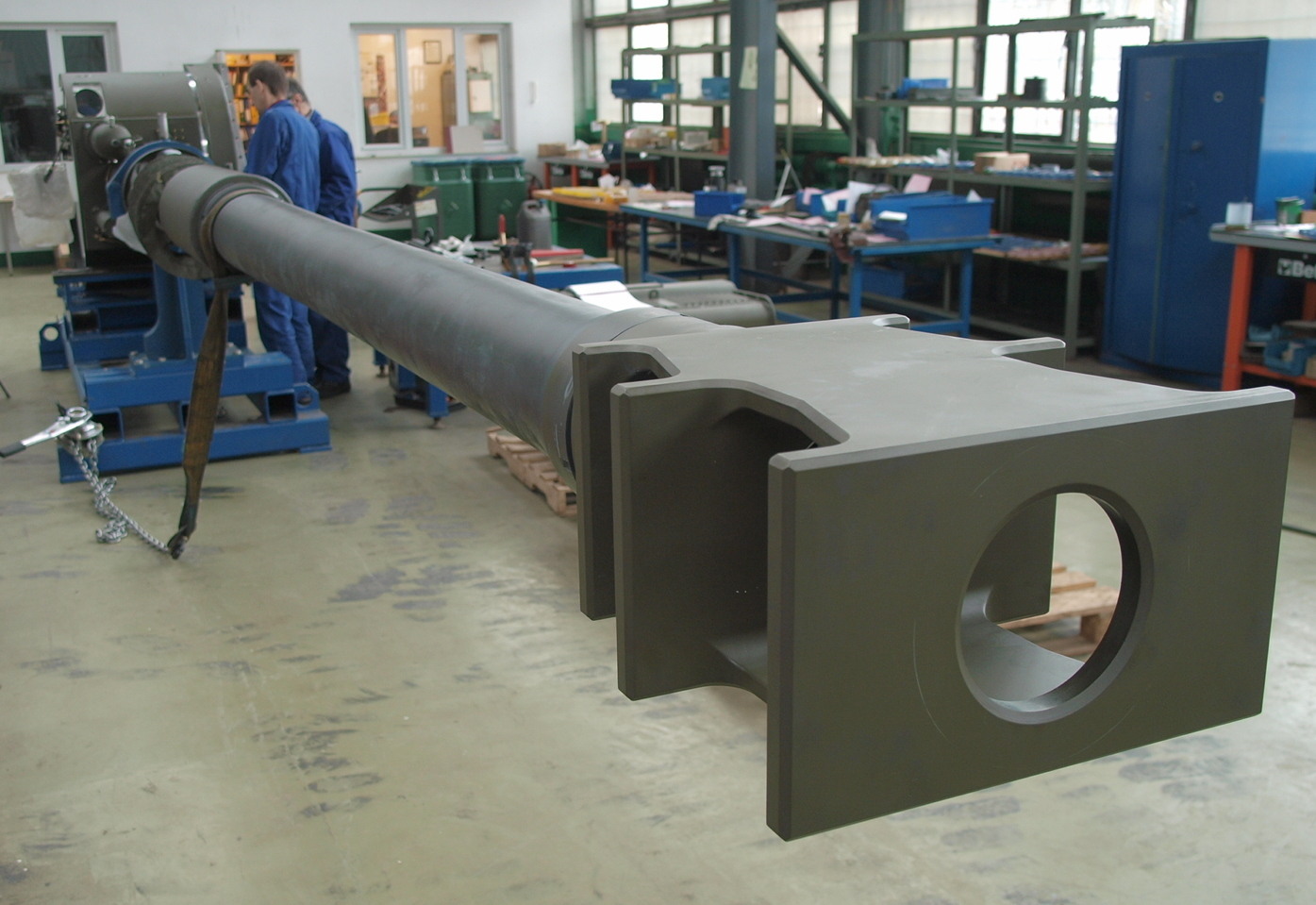
Jak wiadomo, po prezentacji w latach 2000-2001 dwóch prototypów Kraba (początkowo nazywanego Chrobry, co było swobodnym przekładem brytyjskiego Braveheart), i po pomyślnym przeprowadzeniu ich badań (2002-2003) program, kolokwialnie mówiąc, „zawisł, z perspektywą zamknięcia”, a prototypy miały trafić do muzeum. Za sprawą różnych „tricków” udało się anulować ten wyrok śmierci i program, już jako DMO Regina, wznowić. Tyle, że w międzyczasie zmienił się cały biznesowy kontekst; brytyjski partner, nie mogąc doczekać się na przeciągające się decyzje strony polskiej, poczuł się zwolniony z kontraktu produkcyjnego i radykalnie przeorientował swój potencjał techniczny, złomując po prostu oprzyrządowanie produkcyjne przystosowane do produkcji wież AS90 oraz dział do nich.
HSW musiała szukać „planu B”, czyli od podstaw zbudować potencjał zdolny wypełnić tę lukę. W miarę szybko udało się pozyskać kompetencje w zakresie wymiany wyposażenia elektronicznego, oprogramowania komputerów wieży itp., oraz produkcji korpusów wież i większości elementów działa. Ale nie było to łatwe w odniesieniu do luf, wymagających stosowania złożonych technologii. Wówczas pojawiła się koncepcja współpracy z firmą Nexter, od której kupiono pewną partię luf, oraz współpracy z Rheinmetallem. Ta firma nie tylko dostarczyła partię gotowych luf dla pierwszego, wdrożeniowego DMO (jego pierwszą baterię przekazano pod koniec 2012 r.), ale też wsparła HSW w zakresie produkcji tych podzespołów i elementów, które wymagały stosowania technologii, jakimi HSW nie dysponowała. Np. do wykonywania zamka i nasady działa konieczne było stosowanie technologii elektrodrążenia, którą pozyskano już w trakcie produkcji Kraba.
Kooperacja z partnerem znad Renu pozwoliła spokojnie i systematycznie modernizować i rozbudowywać lufownię, a jednocześnie realizować produkcję Kraba. Na dostawy niektórych zamówionych maszyn i urządzeń trzeba było oczekiwać kilkanaście miesięcy, i ten czas „kupiła” dla HSW współpraca z niemieckim partnerem, która obecnie wchodzi na nowy poziom. Stąd nie dziwią słowa prezesa Rheinmetall Waffe Munition GmbH Romana Koehne wygłoszone 21 lipca: – Podpisana dziś umowa to kolejny krok w rozwoju naszej współpracy z HSW, z której jesteśmy bardzo zadowoleni. Huta Stalowa Wola to profesjonalny partner i jesteśmy gotowi do dalszego jej rozszerzania na kolejne typy nowoczesnego uzbrojenia czołgowego.
W dziedzinie uzbrojenia czołgowego HSW SA ma tradycje, o których mało kto pamięta, a które sięgają roku 1953, gdy Polska uruchomiła licencyjną produkcję czołgów T-34/85. Armaty do nich, w ówczesnej nomenklaturze noszące nazwę S-6, produkowała właśnie HSW. Legendarnych czołgów (a więc i armat do nich) wyprodukowano w Polsce, także na eksport, ok. 1400, luf 85 mm – znacznie więcej. Równolegle w tym okresie produkowano także inne typy uzbrojenia artyleryjskiego, haubice ciągnione 122 mm (M-30, czyli S-1), armaty przeciwpancerne 85 mm (D-44, oznaczana jako S-7), armaty przeciwlotnicze 85 (KS-12, znana jako S-3) i 100 mm (ta ostatnia, typu KS-19, w latach produkcji w HSW, czyli 1956-1959, nosząca kryptonim S-9, dysponowała lufą o długości ponad 6 metrów). Prawdziwym przebojem HSW w dziedzinie armat czołgowych była, produkowana aż do lat 90., armata D-10T kal. 100 mm do czołgów T-54/T-55 mająca lufę o długości ponad 5,6 metra. Czołgów tego typu wyprodukowano w Polsce ok. 5 tysięcy, armat i luf do nich – na pewno nie mniej niż 6-7 tysięcy, ale trudno brać pełną odpowiedzialność za tę liczbę; ówczesne informacje na temat skali produkcji i kierunków sprzedaży były ścisłą tajemnicą. Jeśli ktoś nie wie: czołgów z tej rodziny wyprodukowano łącznie ok. 95 tysięcy, używane są one do dziś w wielu krajach, toteż od czasu do czasu pojawiają się zamówienia na części do nich, w tym lufy…
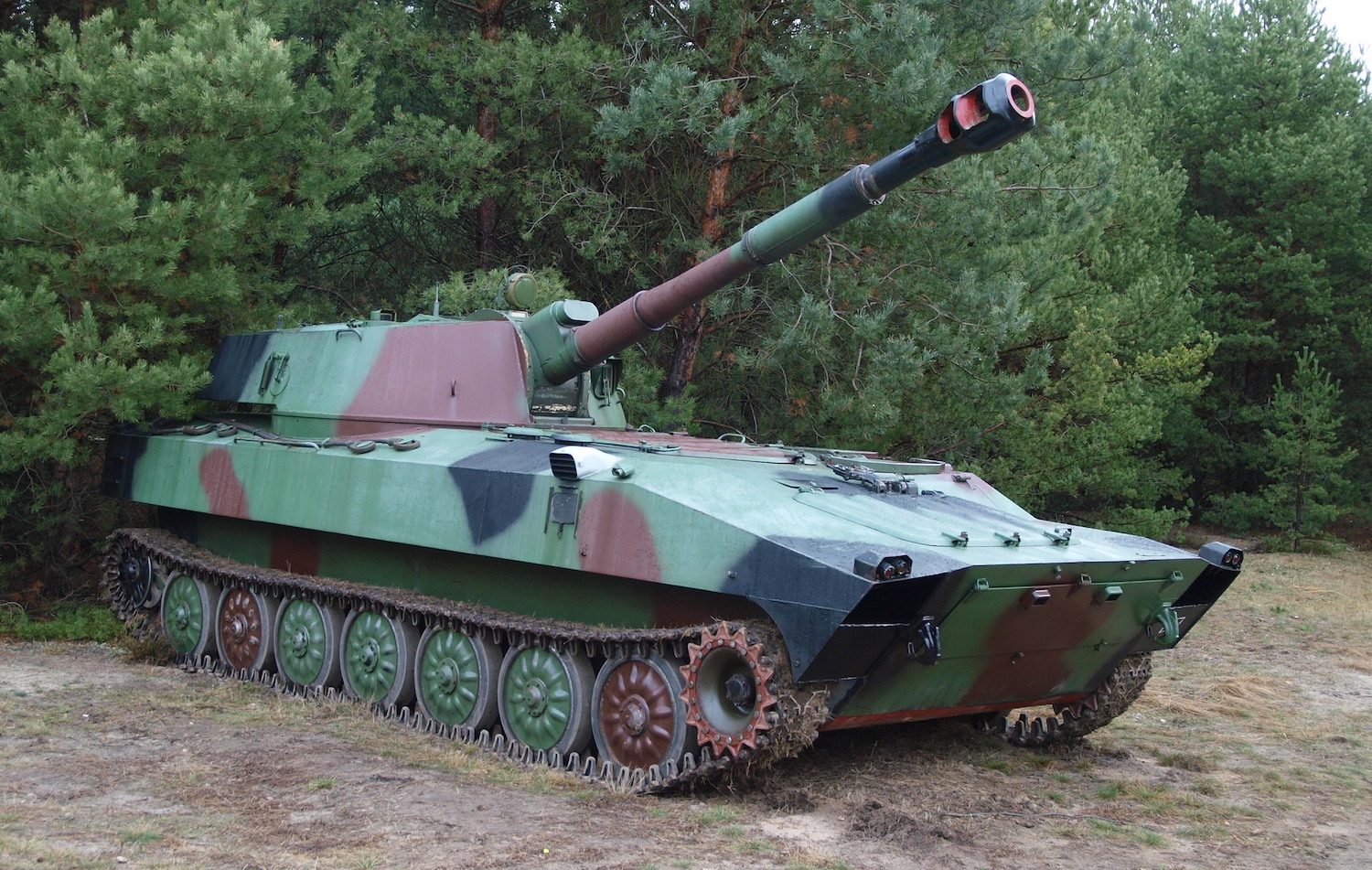
Serię licencyjnych wdrożeń sprzętu artyleryjskiego budowanego w oparciu o wschodnie (radzieckie) licencje i technologie zamknęła w 1983 r. haubica 2A31, stanowiąca uzbrojenie pływającej sh 122 mm 2S1 Goździk, będącej wciąż na uzbrojeniu Sił Zbrojnych RP i zastępowanych przez znacznie potężniejszy i nowocześniejszy system Regina/Krab.
Do czasu transformacji ustrojowej w 1989 r. Huta Stalowa Wola była jednym z bardziej liczących się producentów sprzętu artyleryjskiego, niezwykle cenionym przede wszystkim za najwyższą jakość wykonania i niezawodność swoich wyrobów. Choć w latach PRL nie było mile widziane odwoływanie się do tradycji II Rzeczypospolitej, ówczesna pozycja HSW jednoznacznie nawiązywała do tradycji Zakładów Południowych, zbudowanych w Stalowej Woli w ramach Centralnego Okręgu Przemysłowego. Jednym zdaniem: budowę ZP rozpoczęto wyrębem dziewiczego lasu 20 marca 1937 r., już 7 kwietnia 1938 r. na zakładowej strzelnicy przestrzelano pierwsze zmontowane w ZP działa kal. 100 mm, wiosną 1939 r. ruszyła produkcja seryjna haubic 100 mm (16 szt. miesięcznie) oraz armat 75 i 105 mm, 14 czerwca 1939 r. ukończone i wyposażone Zakłady uroczyście otworzono i poświęcono, a 14 września zostały one zajęte przez Niemców i po niedługim czasie włączone do Hermann Goering Werke jako Werk Stalowa Wola.
Czytaj też: Ukraść Goeringowi… Acht komma Acht!
Do wybuchu wojny w ZP, zatrudniających już 3,6 tys. pracowników, zdołano wprowadzić do produkcji lufy, bądź kompletne działa, w kalibrach od 37 mm (armata przeciwpancerna Boforsa) i 40 mm (armata przeciwlotnicza Boforsa) poprzez 75 i 100 mm, po, jak planowano, armatę 155 mm, haubicę 200 mm i ciężki moździerz kal. 320 mm. W czasie okupacji wytwarzano tutaj m.in. kompletne działa 88 mm i części, w tym lufy, do nich. Tak przed wojną, jak i w jej trakcie i aż do lat 90. obecna HSW zaliczać się mogła do europejskiej I ligi w produkcji artyleryjskiej. Od 1999 r. konsekwentnie do niej powraca.
Wznowienie w HSW produkcji artyleryjskiej, przy okazji produkcji sh 155 mm Krab i samobieżnego moździerza automatycznego SMK120 Rak (a wcześniej – rodzimej konstrukcji moździerzy holowanych M98 i M120 oraz licencyjnych armat Oerlikon KDA-35 dla PZA Loara, a następnie dla armat A-35/AM-35/AG-35), rozłożono na lata. W pierwszej kolejności wymagało to weryfikacji technicznej, remontów i modernizacji części parku maszynowego z okresu największej świetności produkcji artyleryjskiej, a w dalszej – wyposażenia oddziału produkcji luf w nowe kompetencje techniczne, a więc i nowe obrabiarki i nowe technologie.
Od 2014 do 2017 r. wydano na nie blisko 34,5 miliona złotych (w tym 20 milionów stanowiła pomoc Skarbu Państwa nie będąca pomocą publiczną w świetle przepisów prawa unijnego), a w latach 2018-2020 – kolejnych 16,4 miliona. Tylko na prace badawczo-rozwojowe związane z produkcją artyleryjską, a także na doskonalenie kwalifikacji kadr, wydano w ostatnich latach ponad 3 miliony złotych. Wszystko to stworzyło potencjał, który okazał się i atrakcyjny, i przekonujący dla niemieckiego partnera, który nie kryje, że swojego zainteresowania współpracą z HSW nie ogranicza tylko do luf L44. Prezes Rheinmetalla deklaruje, że współpraca ta będzie możliwa w przypadku podjęcia przez MON decyzji o uzbrojeniu polskich czołgów w nowe typy armat 120 lub 130 mm.
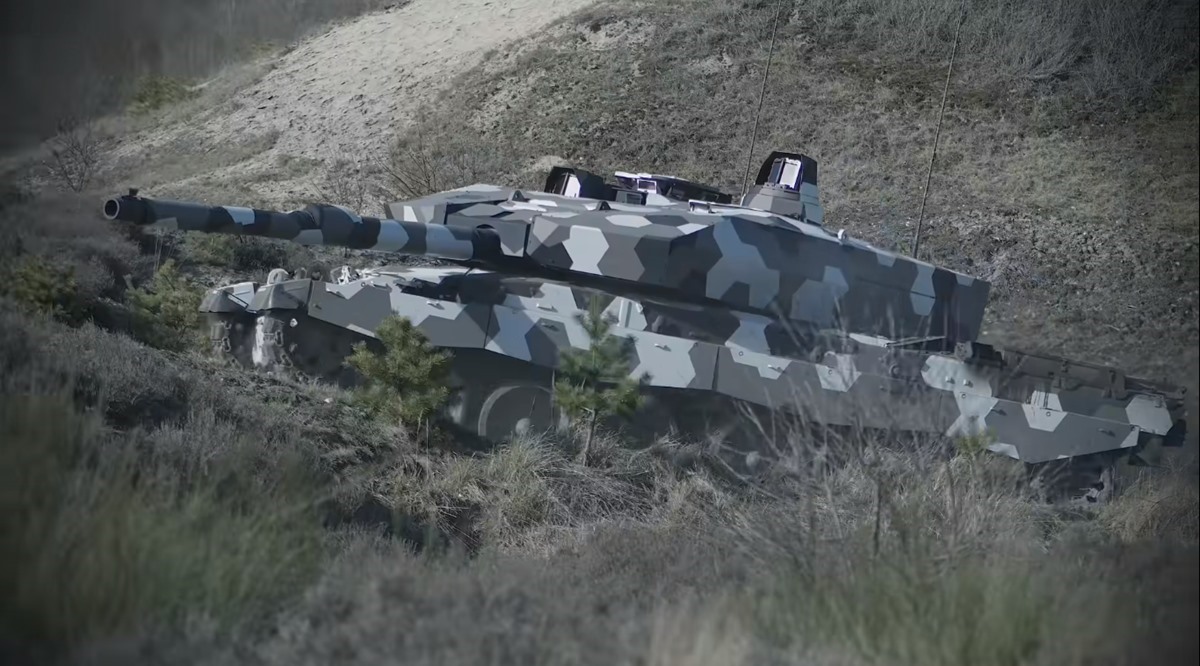
To oznacza otworzenie drzwi zarówno do produkcji luf, a może nie tylko luf, armaty Rh120/L55 oraz, być może, nowej armaty opracowywanej jako jedna z propozycji dla przyszłego euroczołgu, który projektują wspólnie Niemcy i Francuzi w oparciu o zawiązaną w lipcu 2015 r. spółkę joint venture. Czołg Main Ground Combat System (MGCS) docelowo ma zastąpić zarówno Leclerca jak i Leoparda. Nowa armata, Rh130/L51, od 2016 r. już jest promowana, m.in. w brytyjskim czołgu Challenger 2. Rheinmetall deklaruje, że nowa „stotrzydziestka” może być zabudowywana we wszystkich czołgach Leopard 2.
Czytaj też: Armata 130 mm w ogniu
To, czy i w jaki sposób kontynuowany będzie program nowego czołgu Wilk po decyzji o pozyskaniu partii czołgów Abrams jest kwestią otwartą, jednak Ministerstwo Obrony Narodowej deklaruje, że projekt Wilk ma być kontynuowany. Zakup Abramsów dla jednej dywizji nie rozwiązuje przecież problemu wymiany wszystkich T-72 i PT-91 w pozostałych jednostkach. To, jak będą kształtowane dalsze kroki dotyczące modernizacji Wojsk Pancernych i jaka będzie rola polskiego przemysłu, zależy jednak od decyzji politycznych.
Faktem jest, iż obecnie możliwości techniczne i technologiczne HSW SA związane z produkcją artyleryjską są „ustawione” na światowym poziomie. Obróbką z najwyższymi standardami jakości mogą być poddawane elementy o długości do 11 metrów i średnicy wewnętrznej do 800 mm. Nikt nie produkuje dział o takich parametrach, ale wyposażenie techniczne i zdolności technologiczne lufowni mogą służyć nie tylko produkcji artyleryjskiej, ale również np. produkcji precyzyjnych elementów hydrauliki siłowej dla różnych gałęzi przemysłu. Ale podstawowym zadaniem lufowni jest produkcja artyleryjska.
Specjalnie dla potrzeb tej produkcji system technologiczny lufowni wzbogacony został o stanowisko autofretażu. Jest to, mówiąc w największym uproszczeniu, technologia utwardzania powierzchni wewnętrznej przewodu lufy, czyli zwiększania jej odporności na ścieranie, a tym samym żywotności, poprzez mechaniczne zgniatanie warstwy powierzchniowej metalu z wykorzystaniem ekstremalnie wysokiego ciśnienia hydraulicznego rzędu 10 tys. barów. Ta technologia będzie zastosowana w przypadku luf do Rh120, w dodatku – w połączeniu z technologią utwardzania powierzchni luf poprzez chromowanie. Te połączone procedury technologiczne będą stosowane tak w odniesieniu do luf gładkościennych (co ma miejsce w przypadku luf do Rh120 czy, być może, także SMK120 Rak), jak i bruzdowanych (w odniesieniu do luf 155 mm do Kraba i Kryla, armaty KDA-35 oraz, po uruchomieniu produkcji tej armaty w HSW, najprawdopodobniej także ATK 44 Bushmaster Mk44S dla wieży ZSSW-30).
Obecnie praktycznie jedynym nie będącym pod kontrolą HSW elementem procesu produkcyjnego luf długich jest produkcja półfabrykatu hutniczego, czyli wstępnie rozwierconych i obrobionych cieplnie odkuwek, z których drogą obróbki mechanicznej są wykonywane lufy. Takie półfabrykaty w Europie wykonuje zaledwie kilka wyspecjalizowanych hut, które można zliczyć na palcach jednej dłoni. Jeszcze kilka lat temu analizowano możliwość uruchomienia w polskim przemyśle także i takich zdolności. Rozważano wspólną z Hutą Stali Jakościowych w Stalowej Woli inwestycję w te kompetencje techniczne. Pomysł upadł, nie tylko dlatego, że zadziałały pozatechniczne argumenty (HSJ, w przeszłości serce Zakładu Hutniczego HSW, należy do prywatnego inwestora, jakim jest Grupa Cognor), ale również analiza ekonomiczna.
Kompleks, pozwalający na wytwarzanie i pełną obróbkę tej wielkości odkuwek na lufy artyleryjskie, musiałby kosztować ok. 40 milionów złotych, wydanych m.in. na budowę odpowiedniej wielkości pieców wgłębnych, wdrożenia wymaganej licencją na lufy 155/L52 technologii przetopu elektrożużlowego itp. To jest kwota, którą porównywać można ze wszystkimi dotychczas poniesionymi, od 2014 do 2020 r., wydatkami na rozbudowę, wyposażenie i modernizację lufowni (50,7 miliona zł). Poza gigantycznym kosztem tej inwestycji otwartą kwestią pozostaje jeszcze tzw. efekt skali. To, co ma ekonomiczny sens przy produkcji liczonej setkami egzemplarzy luf w cyklu rocznym (a tak było w przypadku wyrobów artyleryjskich wytwarzanych w HSW do lat 90.), traci sens przy skali zamówień o rząd wielkości niższej.
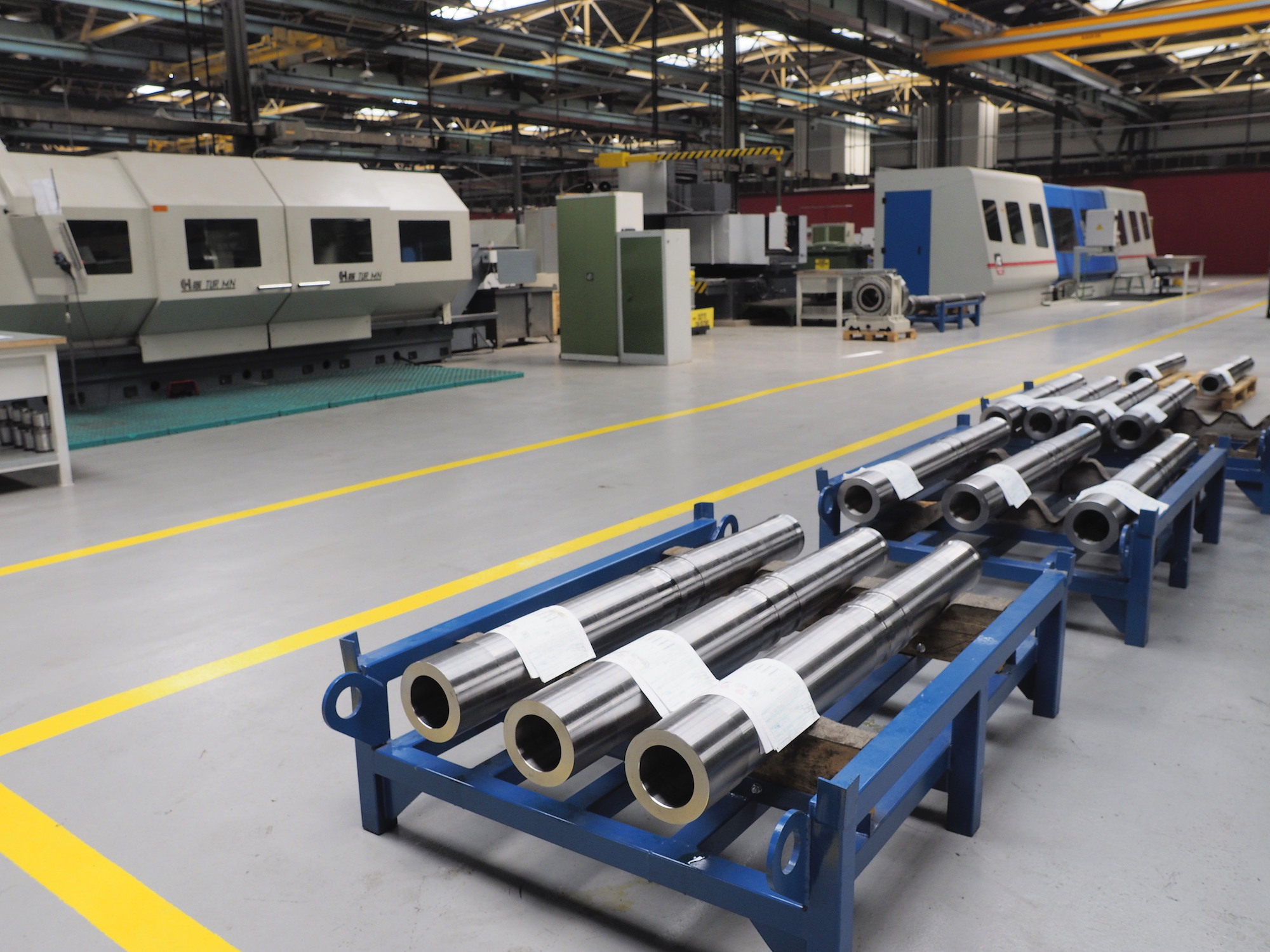
Nie zapominajmy, że obecnie (do 2024 r.) HSW realizuje kontrakty opiewające na 120 Krabów i 120 Raków, w przyszłości dojdzie jeszcze prawdopodobnie około 100 Raków i być może kolejne Kraby. Po sfinalizowaniu produkcji armaty 30 mm dla wieży bezzałogowej, dojdzie do tego wolumenu kilkaset luf znacznie mniejszych kalibrów, które nie wymagają poniesienia tak dużych nakładów na pozyskanie komponentu hutniczego. Tak się już dzieje w przypadku wsadu na lufy dla Raka, mające jednak nie ponad 8, nie 6, ale 3 metry długości. W przypadku luf długich najkorzystniejszym będzie kupowanie gotowych półfabrykatów u wyspecjalizowanego zagranicznego dostawcy, być może u tego samego, u którego zaopatruje się... sam Rheinmetall.
W latach minionych kiedy w skład Kombinatu Przemysłowego Huta Stalowa Wola zatrudniającego ok. 25 tys. pracowników, wchodził wspomniany Zakład Hutniczy, takie decyzje inwestycyjne podejmowano. W przypadku produkcji sh Goździk inwestycją taką był system COS (Ciągłe Odlewanie Stali), dzięki czemu w HSW uzyskiwano odpowiednie ilości wysokiej jakości stali nie tylko na lufy haubicy 2A31, ale też na blachy i płyty pancerne. Te zresztą HSJ produkuje nadal, m.in. dla potrzeb produkcji KTO Rosomak. Ale półfabrykatów hutniczych na lufy Leoparda oraz Kraba i Kryla, nawet te o długości 52 kalibrów, czyli nieco ponad 8 metrów (o ile, w ramach rozwoju tych dział nie zostaną wdrożone w przyszłości lufy o długości 56 kalibrów, albo nawet 60 kalibrów, czyli 9,3 m) tu się wykonać nie da bez wspomnianych inwestycji o kilkudziesięciomilionowej wartości. Pozostawmy bez odpowiedzi pytanie o to, po jakiej ilości wyprodukowanych luf zwróciłyby się poniesione na inwestycję tego rodzaju nakłady.
Skoro już jesteśmy przy zagadnieniu gabarytów wykonywanych w HSW luf artyleryjskich, to warto powtórzyć: już ponad 40 lat temu tutejsza lufownia, dysponująca znacznie skromniejszym parkiem maszynowym, wykonywała obróbkę luf o długości do ponad 6 metrów, czyli znacznie dłuższych niż Leopardowe L44 (5,28 m), porównywalnych z dłuższą o 1,32 m lufą L55 do Rh120 a nawet lufą L51 do Rh130 (6630 mm). Z pewnością na przeszkodzie nie staną także masy tych luf, nieporównanie mniejsze od masy „klepanych” seryjnie luf 155/L52 do Kraba i Kryla (lufa L44 waży 1190 kg, L55 – 1347 kg, lufa do Rh130/L51 – 1400 kg). Nie ma zatem najmniejszych problemów technicznych, aby podjąć się także obróbki luf L55, o ile zamówi je w Stalowej Woli Rheinmetall. Na razie nie wiadomo bowiem o planach zakupu czołgów z „długimi” lufami dla Wojska Polskiego.
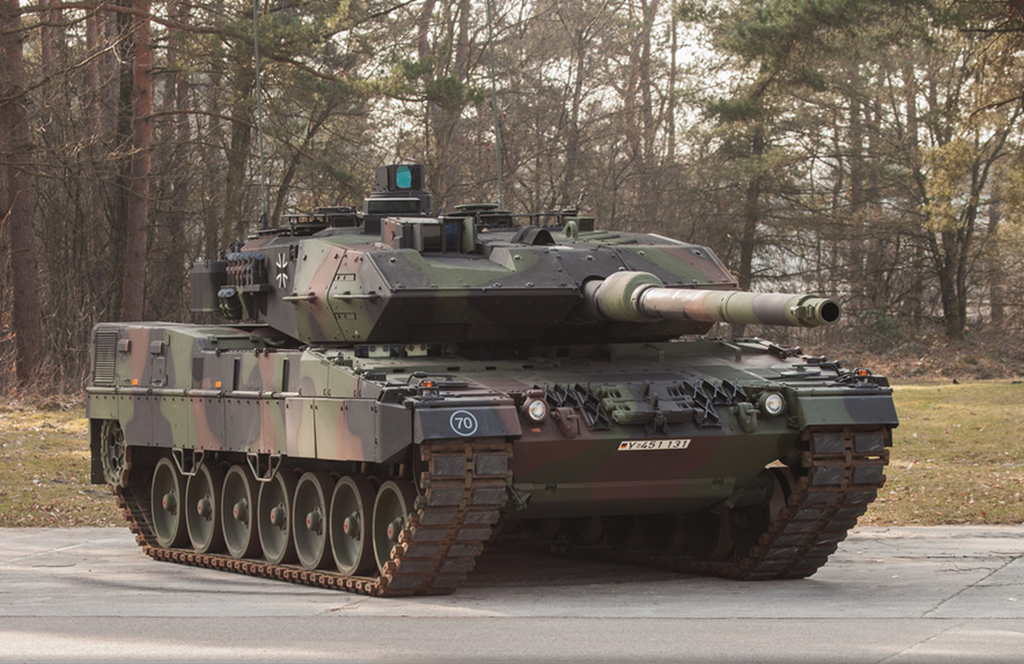
Co do nowej armaty 130 mm, dedykowanej od samego początku dla nowego czołgu, który dopiero ma powstać, jest możliwa – przynajmniej tak deklaruje Rheinmetall – ewentualna opcja „upgrade`u” wszystkich dotychczasowych wersji Leoparda 2. W praktyce musiałoby się to odbywać w ramach współpracy z partnerem (partnerami) niemieckimi, na przykład poprzez integrację na Leopardzie nowej wieży, zaprezentowanej przez Rheinmetalla dla Challengera 3. Nad głęboką modernizacją Leoparda, oznaczoną Leopard 2 aX, pracuje też KMW i jak pisał EDR Magazine, nie wyklucza się integracji nowej wieży (co z kolei otworzyłoby drogę dla potencjalnej wymiany uzbrojenia głównego), aczkolwiek nie jest to przesądzone. Oczywiście każda głęboka modernizacja Leopardów to również integracja wielu innych nowych systemów, w tym łączności, kierowania ogniem/BMS, być może także aktywnej ochrony. Na razie jednak w Polsce używane mają być czołgi z armatami w wersji L44 (dodajmy, że dostosowane jednak do nowszej amunicji przeciwpancernej klasy DM-63, dotyczy to zarówno Leopardów 2PL po modernizacji, jak i Leopardów 2A5). To, czy i w jakim kierunku będą one dalej głęboko modernizowane, jest na razie kwestią otwartą.
Do spekulacji, że lipcowa umowa pomiędzy HSW SA a RWMG może przybliżyć do rozwiązania kwestii wymiany luf w Abramsach, które dopiero mają zostać zakupione, też dziś należy podchodzić z bardzo dużą rezerwą. Dlaczego? Armata M256, choć spokrewniona zasadniczo z Rh120/L44, jest jednak inną konstrukcją, i nie ma zbyt wielu szeroko dostępnych informacji o szczegółach konstrukcji armat. W tym o takich detalach jak skład stopu, z którego wykonywana jest lufa, technologia jego obróbki cieplnej, technologia utwardzania lufy, nie wspominając już o tym, że w Europie i w USA obowiązują nieco inne systemy miar (metryczny vs calowy) oraz norm technicznych.
Co ważne wreszcie – w stosunku do M256, czyli uzbrojenia Abramsa, wszelkie prawa ma nie Rheinmetall, ale ich amerykański producent, i to on będzie rozgrywającym w ewentualnym pozyskiwaniu przez polską stronę praw do działań serwisowych na różnym poziomie. Wreszcie – „nasze” Abramsy, jeśli do Polski trafią, będą traktowane jak wozy nowe, zatem należy przyjąć, iż będą objęte odpowiednią gwarancją (co wyklucza ingerencję użytkownika w konstrukcję wozu przez określony czas), a przede wszystkim, w odróżnieniu od używanych Leopardów 2, będą „fabrycznie nowe”. Czyli – ich armaty nie będą wymagać wymiany luf w perspektywie co najmniej kilku, może kilkunastu lat.
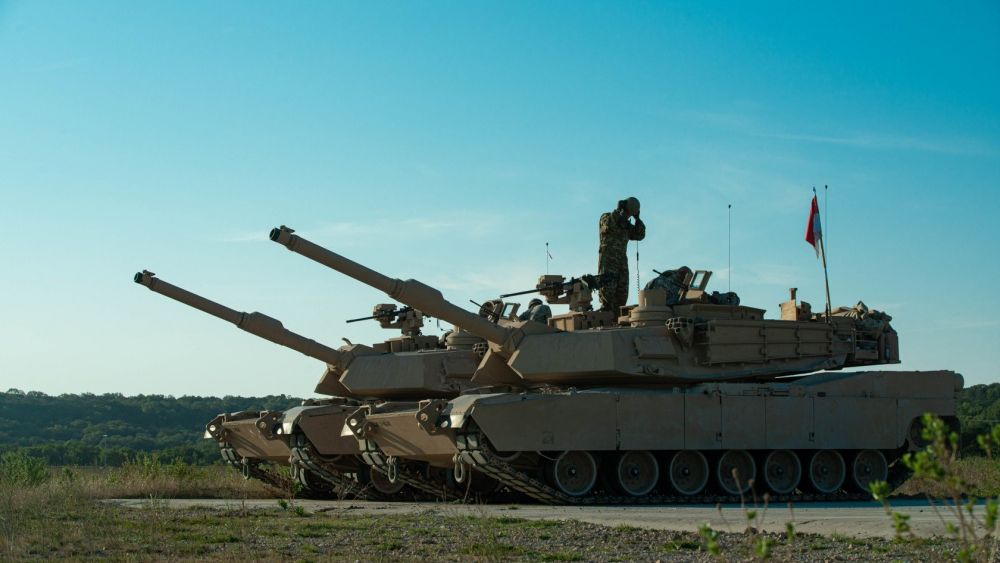
Te wszystkie zastrzeżenia nie zmieniają jednak faktu podstawowego: lipcowa umowa o pozyskaniu przez HSW SA zdolności do wykonywania luf do czołgów tej klasy co Leopard 2, a domyślnie – także Abrams, powinna być dla MON czytelnym sygnałem o tym, w jak szerokim zakresie może w tej dziedzinie polegać na zdolnościach rodzimego przemysłu zbrojeniowego. Ta informacja powinna pomóc w ewentualnym negocjowaniu tego aspektu hipotetycznej transakcji czołgowej z Abramsami w roli podmiotu. Nawet, jeśli zostanie wykluczone, iż możliwe będzie ewentualne zastąpienie lufy armaty M256 lufą L44 wykonaną w HSW na podstawie dokumentacji niemieckiej.
Dla Huty Stalowa Wola SA wejście w tak zaawansowaną współpracę z Rheinmetall Waffe Munition GmbH, włączenie się w łańcuch dostawców niemieckiego koncernu, oznacza także otworzenie nowych możliwości rozwoju biznesowego. Spółka, przypomnijmy, w roku 2020 uzyskała 830 mln zł. przychodów przy zysku netto ponad 59 mln zł., przy czym przychody ze sprzedaży eksportowej wyniosły ok. 60 mln zł. Realizacja zamówień na lufy L44 dla Rheinmetalla stwarza realną opcję wzrostu zarówno sprzedaży, jak i wpływów z eksportu. Czym innym jest bowiem samodzielna walka o swoje miejsce na światowych rynkach, a czym innym – działanie w zespole z silnym, doświadczonym w tego rodzaju operacjach graczem „ligi światowej”.
Jak do tej pory zaliczającymi się do światowej czołówki partnerami HSW w jej obecnym programie produkcyjnym są Raytheon (program Wisła, czyli wyrzutnie rakiet Patriot), Hanwha Techwin (podwozie K9PL/PK9 do sh Krab), Rheinmetall Waffe Munition GmbH (armata Rh120), Tatra (nowy pojazd 4x4, który będzie mieć swą premierę za kilka tygodni), a w bliskiej przyszłości Northrop Grumman (armata 30/40 mm Bushmaster Mk44 dla ZSSW-30). W tym ostatnim przypadku, choć pierwotnie przewidywano pozyskanie technologii w ramach offsetu, to można postawić taką prognozę, że zostanie to rozwiązane drogą samodzielnego ułożenia sobie przez HSW SA relacji biznesowych z amerykańskim partnerem. W tym akurat spółka ma dobrze rokujące doświadczenia.
Artykuł przygotowany we współpracy z HSW S.A.
Wojmi1
ciekawe czy po zapłaceniu rachunku za wodę i energię elektryczną oraz węgiel... po cenach niemieckich coś by zostało jako zysk...
Krzysiek
Bardzo dobry i treściwy artykuł (w zasadzie mała książeczka). Dobrze, że Autor wspomniał o Zakładach Południowych w ramach COP, który dały początek HSW. Wielkie dzieło niezwykle zasłużonej postaci w naszej historii - chemika i polityka gospodarczego II RP, Eugeniusza Kwiatkowskiego. To ten od portu w Gdyni, przypomnę.