Polskie mundury dla Europy i żołnierzy na granicy [WYWIAD]
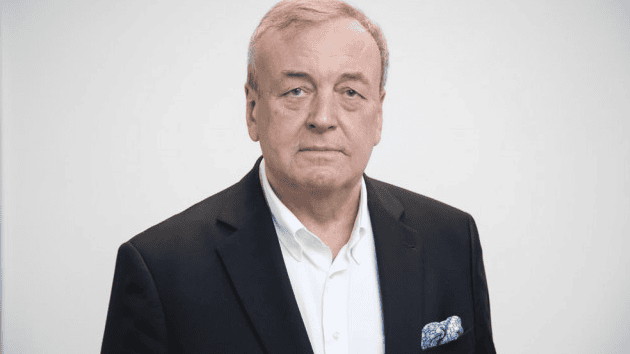
Autor. Federacja Przedsiębiorców Polskich
Posiadamy właściwie sprawdzone rozwiązania oparte na oczekiwaniach czy na dokumentach przetargowych z różnych krajów na świecie. (…) Mamy nadzieję, że zamawiający doceni nasze doświadczenie i wspólnie skonstruujemy odzież nowej generacji - podkreśla w rozmowie z Defence24.pl Andrzej Tabaczyński, Prezes Zarządu Grupy Arlen. Mówi także o wyzwaniach związanych z dostarczaniem umundurowania dla Sił Zbrojnych RP.
Jędrzej Graf, Michał Górski: Grupa Arlen posiada silną bazę produkcyjną w Polsce. Jakie są to zakłady? Ilu ludzi zatrudnia firma? Jakie moce produkcyjne posiadacie?
Andrzej Tabaczyński, Prezes Zarządu Grupy Arlen: Obecnie Grupa Arlen posiada trzy zakłady produkcyjne produkujące odzież. Mowa o zakładzie produkcyjnym Arlen Żyrardów, firmie Tailor -ATG w Dzierżoniowie oraz Arlen Tec w Tarnowie. Te trzy zakłady w 100 proc. należą do firmy Arlen i zatrudniają obecnie około 500 osób. Mowa głównie o szwaczkach, osobach pracujących w działach przygotowania produkcji - pracownikach zatrudnianych w krojowniach, w dziale zaopatrzenia, w magazynach i oczywiście w kontroli. Do Grupy Arlen należy również firma Optex S.A, produkująca tkaniny specjalistyczne. Jest to pewnego rodzaju perła w koronie, ponieważ bez tej firmy dalszy dynamiczny rozwój całej grupy byłby niemożliwy.
Najbardziej istotnym elementem łańcucha dostaw jest dostęp do surowców. W tym przypadku mowa o dostępie do tkanin wysokospecjalistycznych. Optex produkuje tkaniny techniczne. Są to przede wszystkim laminaty dwu- i trzywarstwowe, softshelle, tkaniny trudnopalne oraz antystatyczne. Optex produkuje również specjalistyczne dzianiny – posiadamy własną dziewiarnię, produkujemy od przędzy do gotowej tkaniny - włącznie z laminacją i drukiem, gdzie uzyskujemy remisję w podczerwieni.
Na podkreślenie zasluguje fakt, że cykl produkcji zaczyna się od produkcji przędzy, następnie odbywa się produkcja osnów i procesy tkackie z wykorzystaniem około 150 nowoczesnych krosien, barwienie i wykończenie oraz finalnie druk kamuflażu maskującego z parametrami remisji w podczerwieni. Ostatnim etapem jest laminowanie membranami PTFE lub PU. Cały ten proces odbywa się w firmie Optex. Na podkreślenie zasługuje fakt, że przeprowadzenie całego procesu produkcji tkanin technicznych jest niespotykane i unikalne w Europie.
Czy to jest opracowywane w laboratoriach Grupy Arlen?
Cały rozwój produktu ma właśnie miejsce w Optexie. Dziękuję, że Pan przypomniał o własnym laboratorium – bez niego nie ma nowoczesnej i dobrej jakościowej produkcji. Uważam, że wyposażenie naszego laboratorium jest w tej chwili na porównywalnie dobrym poziomie w stosunku do najlepszych laboratoriów w Europie.
Arlen jako grupa ma bardzo szeroką gamę produktową. Jakie znaczenie dla Państwa ma doświadczenie w produkcji dla Sił Zbrojnych i służb mundurowych? Na ile był to bodziec do rozwoju sprzedaży eksportowej?
Doświadczenia zdobyte we współpracy z Wojskiem Polskim umożliwiły nam na skuteczne konkurowanie na rynkach europejskich. Dzięki temu, że byliśmy zmuszeni do rozwoju produktu, skutecznie wygrywamy przetargi na Litwie, w Norwegii, Szwajcarii, itd.
Przy pracy z wojskiem interesują nas głównie tkaniny specjalistyczne, techniczne, o bardzo wysokich parametrach użytkowych. Jeśli mówimy np. o funkcjonalności, to nasze produkty mogą skutecznie konkurować z powszechnie znanymi tkaninami. Wszyscy znamy firmę Gore-Tex – jest ona pewnego rodzaju wyznacznikiem, podobnie jak wzorzec metra z Sevres. Nasze tkaniny uzyskują dokładnie takie same parametry, jak najlepszej jakości tkaniny wspominanej firmy. Dzięki produkcji w Polsce, na samej różnicy w cenie zamawiający zaoszczędził moim zdaniem około 300 mln zł w ciągu ostatnich 10 lat. Jest to jedyny produkt tekstylny z Polski, stanowiący obecnie skuteczną konkurencję w przetargach dla służb mundurowych. Jesteśmy z tego naprawdę dumni.
O jakich parametrach mowa?
Odporność na słup wody 20 metrów oraz paroprzepuszczalność - czyli współczynnik oporu przenikania pary wodnej poniżej ośmiu. Jest to absolutnie porównywalne z najwyższymi standardami światowymi. Produkujemy między 600 a 700 tys. metrów bieżących tkanin laminowanych.
Do ilu krajów Arlen eksportuje odzież ochronną i specjalistyczną?
To się zmienia, ale dziś mamy kontrakty handlowe praktycznie w całej Europie.
Warto też pamiętać, że rynek odzieży specjalistycznej jest bardzo hermetyczny. Na niektórych rynkach staramy się sprzedawać naszą odzież, na niektórych z kolei jesteśmy dostawcą tkaniny. Na temat konkretnych klientów czy krajów wolałbym się nie wypowiadać – jest to informacja poufna.
Czytaj też
Czy Państwa możliwości i doświadczenia są obecnie w pełni wykorzystywane przez Wojsko Polskie czy służby mundurowe? Na ile byliby Państwo w stanie dostarczyć kurtek czy mundurów jeszcze wyższej jakości? W jakim czasie mogłyby być dostawy?
Jest to bardzo delikatny temat, ponieważ uwzględniając fakt, że firma jest eksponowana na rynki europejskie i bierze udział w zagranicznych przetargach w całym szeregu krajów, wiemy znakomicie, jakie są w tej chwili najnowsze trendy i oczekiwania zamawiających. To dla mnie frustrujące, ponieważ jesteśmy zmuszeni ściśle dostarczać odzież zgodną ze specyfikacją. Problem polega na tym, że ta specyfikacja niejednokrotnie powstawała wiele lat temu i nie uwzględniła ona nowoczesnych rozwiązań – ani konstrukcyjnych, np. możliwości odzieży hybrydowej, ani surowcowych.
Kontynuujemy dostawy odzieży, która naszym zdaniem mogłaby być znacząco lepsza czy bardziej funkcjonalna – i co ciekawe, niekoniecznie droższa. Mogę przytaczać cały szereg przykładów naszych ofert, które w ogóle nie zyskały zainteresowania.
Istnieją problemy w zakresie umundurowania, które Pańskim zdaniem dałoby radę rozwiązać w stosunkowo niedużym odstępie czasu?
Tak, przykład stanowi problem odzieży dla kobiet w Wojsku Polskim. Jest to temat powtarzający się od co najmniej kilku lat, a jest do rozwiązania w trzy miesiące. Pierwsze informacje, że taki problem powstał, uzyskaliśmy sześć miesięcy temu. Zasugerowałem wtedy moje rozwiązanie. Nie wiem, czy powstał chociaż jeden mundur dla kobiet i czy miały miejsce jakiekolwiek próby użytkowe.
Kolejna sprawa dotyczy rozważenia możliwości użycia tkanin na mundury polowe o innym składzie surowcowym. W tej chwili mundur polowy jest skonstruowany z użyciem tkaniny poliestrowo-bawełnianej. Ta tkanina powstała około 20 lat temu, wtedy była uznawana za tkaninę nowoczesną. W chwili obecnej są inne tkaniny o innym składzie surowcowym – znacząco lepsze – zarówno pod kątem funkcjonalnym, użytkowym, ale też ze względu na trwałość.
A czy inne armie świata zamawiają u Państwa te lepsze tkaniny albo mundury?
Ja nie dostarczam mundurów polowych. Koncentrujemy się na produktach specjalistycznych, z tkanin technicznych….
A kurtki lub innego rodzaju odzież ochronną?
Tak, oczywiście. Dostarczyliśmy na przykład 47 tysięcy kurtek dla armii litewskiej, odzież dla oddziałów specjalnych w Anglii, Norwegii itd. Brałem udział w rozwoju całego systemu odzieży ciepłochronnej dla armii indyjskiej. Posiadamy właściwie sprawdzone rozwiązania oparte na oczekiwaniach czy na dokumentach przetargowych z różnych krajów na świecie. Dlatego też obserwuję z ogromną frustracją próby skonstruowania podobnych systemów w Polsce. Trwają one kilka lat i na razie doprowadziły nas według mnie donikąd. Mamy nadzieję, że zamawiający doceni nasze doświadczenie i wspólnie skonstruujemy odzież nowej generacji, a co najważniejsze produkowaną w Polsce, w polskich szwalniach, przez firmy płacące podatki w Polsce. Firma Arlen w 2024 roku odprowadziła 65 mln zł podatków, to znacząca kwota.
Moim zdaniem należy unikać tworzenia skansenów produkcyjnych i zlecania prowadzenia prac badawczo rozwojowych w firmach, które nie posiadają kompetencji. Jaskrawym przykładem jest obecna sytuacja drastycznego braku kurtek ciepłochronnych dla żołnierzy, pomimo ponad trzyletniego procesu pracy nad tym produktem.
Czytaj też
Wcześniej wspominał Pan w rozmowie z nami, że Arlen produkuje kurtki zimowe na wyposażenie Sił Zbrojnych. Zostaliście o to poproszeni całkiem niedawno. Ile tych kurtek macie dostarczyć i w jakim terminie?
Zostałem poinformowany, że z powodu pilnej potrzeby operacyjnej potrzebne jest na tym etapie minimum 1000 kurtek. Podjąłem się tego praktycznie niewykonalnego zadania – bo od momentu podpisania umowy przez trzy tygodnie dostarczymy 1000 kurtek, które powstaną praktycznie od zera. Jest dla nas bardzo istotne, że kurtki zostały skonsultowane z żołnierzami, czyli ich finalnym użytkownikiem. Każda kieszeń, każde otwarcie i zapięcie zostało przedyskutowane z ludźmi, którzy te kurtki będą nosić. To jest bardzo ważne.
Zamówienie, które zostało zrealizowane z powodu pilnej potrzeby operacyjnej, oznacza że wojsko zostało „zaskoczone zimą”?
Wojsko już wcześniej próbowało skonstruować kurtkę ciepłochronną pod nazwą 130. Wzór 130 to efekt prac badawczo-rozwojowych prowadzonych przez firmę Maskpol przez ponad trzy lata. Jak już wcześniej wspomniałem – moim zdaniem – powstała z tego „kufajka”, o zaawansowaniu technicznym i koncepcyjnym którego ocenę pozostawię bez dalszych złośliwych komentarzy.
Ogłoszony przetarg okazał się nieskuteczny – żadna firma nie spełniła wymagań i w związku z tym wojsko zostało w pewien sposób zaskoczone. Przyszła zima, a kurtki, które miały być w teorii dostarczone w ramach przetargu, nie powstały. To wtedy wojsko zwróciło się do kilku firm – w tym do mojej – z pilną potrzebą operacyjną.
Ponieważ ze mną podpisano umowę to rozumiem, że byliśmy jedyną firmą, która była w stanie sprostać wymaganiom. Na tym etapie podpisaliśmy umowę na 1000 kurtek. W ramach ciekawostki powiem, że w związku z „pilną potrzebą” w ciągu dwóch tygodni od podpisania umowy, dostarczymy 200 pierwszych kurtek. Kolejne 800 dostarczymy w ciągu następnych kilku dni. Łącznie będzie to 1000 kurtek wytworzonych przez trzy tygodnie. Od pozyskania tkaniny do gotowej kurtki - ściśle zgodnie z wymaganiami, sugestiami użytkownika końcowego.
Ten przykład pokazuje zdolności firmy i to, że jesteśmy wertykalnie skonstruowani - produkujemy tkaninę, laminaty, jak również odzież we własnych szwalniach. Nie jesteśmy w żaden sposób ograniczani przez podwykonawców, tym bardziej podwykonawców w Chinach, gdzie czas dostawy wynosi od trzech do sześciu miesięcy i jeszcze trzeba się modlić, żeby pociąg, który ewentualnie będzie jechał nie został zatrzymany w Uzbekistanie czy innym kraju. Podkreślam raz jeszcze - nasza produkcja od tkanin do gotowego wyrobu ma miejsce w Polsce. Zapewniamy zatrudnienie w Polsce i tutaj płacimy podatki.
Arlen ma doświadczenie w realizacji zamówień w trybie pilnym. Jak taka pilność zamówień wpływa na możliwości produkcyjne i na cenę?
To totalnie dezorganizuje produkcję i znacząco podnosi koszty. O tym, że żadna inna firma nie była w stanie podjąć się tego zadania świadczy fakt, że tylko my otrzymaliśmy to zamówienie. Jestem przekonany, że było kilka innych firm, które również były pytane.
Dlaczego zatem ostatecznie zdecydowali się Państwo na próbę podjęcia się tego zadania?
Głównie w jednym celu – chciałem pokazać zamawiającemu, że polski przemysł jest absolutnie zdolny do wykonywania rzeczy niewykonalnych i niemożliwych. Wielokrotnie czytałem i słyszałem – na przykład podczas targów MSPO w Kielcach – komentarze mówiące o niezdolności polskiego przemysłu do sprostania oczekiwaniom. Udowodniłem, że to nieprawda.
Warto w tym miejscu przytoczyć jeszcze inny przykład. Dwa miesiące temu powstała inna pilna potrzeba operacyjna, żeby na granicę dostarczyć peleryny. Również to wykonaliśmy. Pięć tysięcy peleryn zostało wyprodukowanych i dostarczonych. Podobna sytuacja powstała obecnie z kurtkami ocieplającymi, rękawiczkami itd.
Czym jest to spowodowane?
Z prawdziwym żalem dostrzegam brak zrozumienia procesów produkcyjnych. Jako Prezes Związku Polskich Producentów Tekstyliów wielokrotnie w czasie prezentacji pokazywałem w bardzo przystępny sposób jak wygląda cykl produkcyjny odzieży. Aby coś uszyć, konieczne jest posiadanie surowców, czyli tkanin, dodatków itd.
Znamiennym przykładem mogą być tu tkaniny aramidowe. Jedynym producentem włókna, z którego powstaje przędza do produkcji tkaniny Nomex Comfort, stosowana na przykład na kombinezony czołgisty i kurtki pilota, jest DuPont – potężna firma, dla której zamówienie na dwie czy trzy tony przędzy jest totalnie nieistotne w całej polityce koncernu. Czyli jesteśmy tu niejako w roli petentów. Dochodzi do tego jeszcze specyfikowany kolor. Żeby uzyskać przędzę, od momentu zamówienia potrzeba około trzech miesięcy. Można stawać na głowie i straszyć „potęgą polskiej armii”, a i tak nie otrzymamy szybciej przędzy w danym kolorze.
Następnie trzeba tę tkaninę wyprodukować. To jest kwestia minimum sześciu tygodni. Z tego trzeba uszyć kombinezony. Od zamówienia do pierwszej dostawy wychodzi mniej więcej sześć miesięcy, zakładając że zamawiający podpisze umowę i materiał, czyli przędza, będzie dostępna.
Są inne rozwiązania?
Alternatywą jest zakup tkaniny, co wiaże się z ogromną dozą ryzyka, nie wiadomo bowiem, co się stanie dalej z takim przetargiem. Przykłady tego mieliśmy kilka lat temu, kiedy przetargi zostały unieważnione właściwie w przeddzień otwarcia ofert. Obecnie żadna firma w Polsce nie będzie podejmować decyzji, żeby zakupić surowce ze wiele milionów złotych, który będzie później niesprzedawalny.
Teraz pozostaje pytanie, dlaczego firmy, które produkują tkaniny, muszą podjąć ryzyko, żeby zakupić surowiec w chwili ogłoszenia przetargu, a nie czekając na wynik tego przetargu? Z prostego powodu - terminy dostaw kwotowane w przetargach na przykład 120 dni od podpisania umowy, wykluczają jakiekolwiek dostawy gotowego wyrobu. Czyli w tej sytuacji powstała swoista kwadratura koła.
Zadajemy sobie pytanie: w ogóle nie brać udziału w przetargach, czy starać się jednak podjąć ryzyko,biorąc pod uwagę społeczną odpowiedzialność za zatrudnionych ludzi? Bez ryzyka wykonanie tych dostaw w spodziewanym terminie jest totalnie niewykonalne i niemożliwe. Wyłącznie przetargi wieloletnie dają jakąś gwarancję planowania.
Czyli uważa Pan, że cała branża tekstylna w Polsce, która produkuje odzież ochronną na rzecz armii czy służb mundurowych, zyskałaby, gdyby to planowanie rzeczowe było w sposób długofalowy zaplanowane? Towar byłby tańszy?
Na pewno miałoby to wpływ na finalną cenę. Bo jeżeli planuje się zakupy i na przykład wiemy, że będziemy mieć produkcję w roku 2025, to można kupić przędzę w trzecim kwartale 2024, można się przygotować i wykonać tkaninę wcześniej.
Jeśli czeka się do ostatniego momentu, to wiadomym jest, że wykorzystują to dostawcy surowców, bo wiedzą, że wtedy istnieje potężna presja na terminy dostaw, itd. Abstrahując od tego, po prostu należy stwierdzić, że produkcja musi być właściwie planowana.
Wiele firm konkurencyjnych w stosunku do nas, które jednocześnie są członkami naszego związku, mówią często o współpracy na zasadzie absolutnego braku partnerstwa ze strony państwa. Nie można traktować nas jak petentów. Jeśli przetarg jest skonstruowany w taki sposób, że jest zamówienie gwarantowane, a później jest 60 dni na zamówienie opcjonalne to zamawiający może to wykorzystać. Kilka lat temu otrzymałem zamówienie opcjonalne na pięć tysięcy kombinezonów dla czołgistów. Było to na 61 dni przed finalnym terminem dostawy. Zamawiający doskonale wiedział, ile czasu zajmuje zorganizowanie produkcji tkaniny i szycie.
Wspominał Pan o tym, że bierzecie udział w wielu przetargach w Europie. Dostarczacie do różnych armii (i nie tylko) odzież ochronną. W tej chwili mówi się o odbudowie europejskiego przemysłu zbrojeniowego, być może będą jakieś specjalizacje. Czy jako Polski Związek Producentów Tekstyliów, Przemysłu Tekstylnego widzicie też w tych europejskich programach szansę? Czy polski przemysł tekstylny jako taki miałby szansę w zamówieniach dla Europy?
Tak, jak najbardziej. Miałby ogromną szansę pod warunkiem, że będzie to skoordynowane. Natomiast nie możemy zapominać, że konieczna jest wspolpraca miedzy firmami, oparta na wzajemnym zaufaniu i szacunku.
Bez tkanin i bez surowców absolutnie nie ma mowy o jakimkolwiek wejściu na rynek europejski. Gdybyśmy zaczęli działać jako grupa (zakłady Optex, Andropol, szwalnie Arlen, Elremet, firma Wybrzeże) mamy szansę być bardzo poważnym graczem, bo w Europie nie ma firm o takim potencjale produkcyjnym. Mogę też wymienić Maskpol, który dzięki działaniom poprzedniego zarządu ma bardzo dobrą szwalnię w Częstochowie i posiada duże zdolności produkcyjne w granicach 140 tysięcy mundurów polowych rocznie.
Dziękujemy za rozmowę
Potencialny poborowy
Cd Być może membrany z Maskpolu również mają dobre parametry ale w takim przypadku firma powinna również w jasny i szczegółowy sposób zakomunikować to szerszej publiczności by unikać nieporozumień po częstych wpisach żołnierzy o "ceratexach" podróbach GORE-TEX.
Potencialny poborowy
Bardzo zaciekawiło mnie twierdzenie że membrana odzieży Arlen ma takie same lub bardzo zbliżone parametry do GORE-TEX. Jeśli tak jest naprawdę to ogromny sukces polskiej firmy. Do parametrów porównawczych oprócz paro przepuszczalności i wodoodporności dodałbym jeszcze odporność na zginanie czyli wytrzymałość membrany podczas użytkowania. Ciekawe jest Jeszcze czy owe parametry są uzyskane na samej membranie czy na końcowym laminacie z impregnacją. Jeśli na membranie to tylko pogratulować. O konkurencji powinno mówić się dobrze lub wcale ale w tym przypadku można zrozumieć Pana Prezesa ponieważ to co robi się z umundurowaniem w programie Tytan przez Maskpol to już nieśmieszny żart. Przykład był na ostatnich MSPO gdy Pani z Maskpolu podczas wywiadu z FRAG OUT stwierdziła że: ... kurtka ochronna chroni przed lekkim deszczem" Powinno być więcej takich artykułów które w taki sposób rozwiewają wątpliwości co do jakości wyrobów naszych producentów.
Zenek2
Norma - podstawowe słowo betonu w WP. Może być najgorsza, ale to norma i nikt nie może się przyczepić. No i projektowanie kurki zimowej przez 3 lata - to potrafią tylko państwowe firmy i państwowy klient. Miś na miarę naszych możliwości.
Opornik
Na obronę tyle że wojsko i wszystko co z nim związane do tej pory traktowane było jako zbędny ale konieczny koszt więc cięto co się dało i kupowano na sztuki. Niemniej do samego procesu planowania zakupów powinny obowiązkowo być dopuszczone siły cywilne i to one powinny kontrolować zakupy.