Kluczowa rola analiz i symulacji inżynierskich - odwrócenie paradygmatu i zmiana przyzwyczajeń
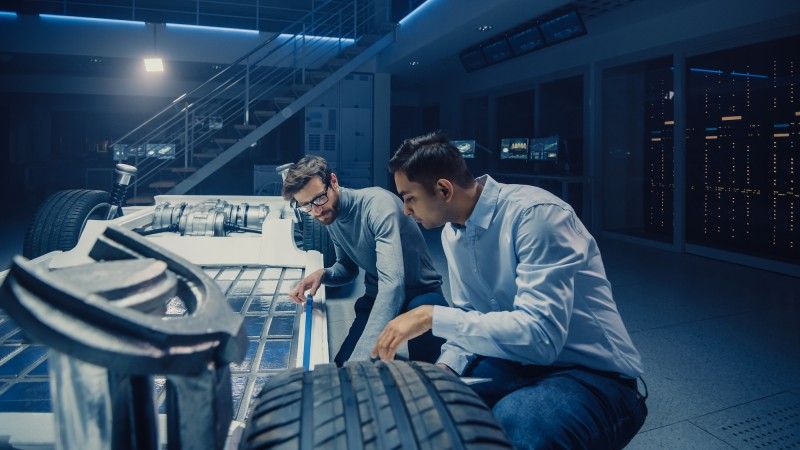
Wzrost, optymalizacja i cyfryzacja - trzy priorytety wskazywane przez przemysł w 2023 roku są ze sobą bezpośrednio skorelowane. Dwa pierwsze stanowią naturalny kierunek rozwoju firm chcących zachować konkurencyjność i szybko reagować na zmieniające się zapotrzebowanie rynku. Cyfrowa transformacja odgrywa z kolei kluczową rolę w osiągnięciu sukcesu w obu tych obszarach. Wykorzystując zaawansowane rozwiązania oferowane przez Siemens Digital Industries Software, sektor obronny może unowocześniać działania, z naciskiem na zmiany w procesach projektowym i konstrukcyjnym z użyciem narzędzi badań i rozwoju.
Artykuł sponsorowany, partner publikacji Siemens Digital Industries Software
Przedsiębiorstwa przemysłowe od lat inwestują w efektywne zarządzanie zasobami, a jednocześnie z dużą ostrożnością podchodzą do technologii cyfrowych i analitycznych wykorzystywanych do projektowania produktów. Zaledwie 35% firm z sektora lotniczego i obronnego, jak podaje McKinsey (1), wykorzystuje tego rodzaju rozwiązania poprawiające jakość i wydajność procesów inżynieryjnych. Czy ostrożność jest wskazana i jakkolwiek uzasadniona?
Rola symulacji - współczesne pole walki dla inżynierów
Projektowanie rozwiązań w sektorze obronnym wiąże się ściśle z konkretnymi wymaganiami dotyczącymi tego, jak końcowy produkt ma funkcjonować. Wytyczne taktyczno-techniczne wyraźnie wyznaczają ramy projektowe, jednocześnie klienci oczekują przyspieszenia procesów projektowych. Inżynierowie poświęcają dużą część czasu i zasobów na dopilnowanie spełnienia ścisłych wymagań dla danych konstrukcji – niezależnie, czy mówimy o pojeździe bojowym, czy elemencie ekwipunku żołnierza.
Tendencja obserwowana obecnie na świecie wskazuje na coraz większe i bardziej świadome wykorzystywanie w organizacjach przemysłowych, możliwości cyfrowych analiz i symulacji. Charakteryzuje się to konsekwentnym odchodzeniem od fizycznych prototypów na rzecz ich wirtualnych odpowiedników. Firmy z sektora obronnego zbierając duże ilości potrzebnych informacji na wczesnym etapie prac projektowych, mogą skrócić czas wejścia produktu na rynek, równocześnie minimalizując koszty i ryzyko niezgodności podejmowanych decyzji w odniesieniu do wytycznych taktyczno-technicznych. To otwiera przed nimi szanse na większą innowacyjność, elastyczność i produktywność, przekładających się na większą dostępność gotowych i nowoczesnych produktów. Wspierany za pomocą cyfrowych rozwiązań proces projektowy, uwzględniający symulacje i analizy, pozwala produkować od razu dobrze i minimalizować problemy charakterystyczne dla wieku dziecięcego konstrukcji i produktu.
Pomimo tych dostrzegalnych zalet obszar symulacji i testów jest nadal słabo rozwinięty w Polsce. Wynika to w dużej mierze z niewielkiej świadomości lokalnych przedsiębiorstw dotyczących możliwości narzędzi cyfrowych. Pokutuje przekonanie, że niezbędne informacje są możliwe do uzyskania wyłącznie podczas czasochłonnych, fizycznych prób prototypu, które do niedawna stanowiły niemożliwy do zastąpienia etap procesu projektowego.
Tymczasem, jak przekonują eksperci Siemens Digital Industries Software, zmiana podejścia do procesu projektowania przekłada się nie tylko na jego większą efektywność, ale również znacznie zwiększa odczuwany przez organizację zwrot z inwestycji.

Zmiana procesu, odwrócenie paradygmatu
Jak wygląda tradycyjny proces projektowy, określony w dużej mierze przez możliwości i ograniczenia organizacji? Zazwyczaj zaczyna się od tak zwanego modelu wstępnego, a więc początkowej konstrukcji powstałej na bazie dotychczasowych doświadczeń projektowych. Eksperci opracowują konstrukcję, która następnie jest sprawdzana pod kątem różnych parametrów, tj. wytrzymałości, akustyki, obciążenia termicznego, elektromagnetyki, konsumpcji energii, dostępnego zapasu mocy itd., zgodnie z wymaganiami taktyczno-technicznymi. Tutaj też firmy napotykają poważną przeszkodę, którą jest ograniczona dostępność osób zajmujących się symulacjami i analizami. To przekłada się na dłuższy czas realizacji zadań symulacyjno-analitycznych, oczekiwania na wyniki i ich interpretację. Często więc zdarza się tak, że konstruktorzy otrzymują wnioski analityczne dotyczące pierwszej rewizji/wersji konstrukcji w momencie, kiedy sami są już przy np. trzeciej iteracji danego projektu, rozwijanego przez cały czas na bazie własnych doświadczeń i wcześniejszych projektów.
Tak funkcjonujący proces badawczo-rozwojowy powtarza się w ramach trwających prac konstrukcyjnych. Czas realizacji symulacji i analiz nie jest adekwatny do postępów projektowych. Skutkuje to sytuacją, w której na rynek może trafić produkt końcowy sprawdzony jedynie częściowo, w którym nawet ok. 30% zaimplementowanych rozwiązań mogła nie zostać zweryfikowana, ze względu na opóźnienia. Łatwo wyobrazić sobie, jakie może mieć to konsekwencje w przypadku wysoko zaawansowanych produktów tworzonych przez przemysł obronny.
Czytaj też
W celu wykorzystania możliwości dostępnych narzędzi cyfrowych, pozwalających na wykonywanie analiz i symulacji na bardzo wczesnym etapie procesu projektowego, specjaliści Siemens Digital Industries Software proponują odwrócenie paradygmatu. W sytuacji kiedy nie dysponujemy jeszcze wstępnym modelem 3D, wdrożyć możemy proces kompleksowych symulacji systemowych. Powinno to zmienić sposób pracy konstruktorów, którzy już na podstawie prostych schematów funkcyjnych są w stanie określić, czy dana konstrukcja będzie spełniała wstępne wymagania zawarte w wytycznych taktyczno-technicznych.
Dostęp do tych danych zapewnia projektantom zupełnie inną pozycję startową. Pozwala pominąć szereg kosztownych ścieżek rozwoju produktu, które dzięki analizom można ocenić z wyprzedzeniem, pod kątem realizacji z pozoru atrakcyjnych pomysłów i niezbędnych do ich wykonania zasobów.
Zmodyfikowany proces, w którym każda kolejna rewizja/wersja jest poddawana analizom i symulacjom, bez opóźnień charakterystycznych dla tradycyjnego modelu procesu badawczo-rozwojowego. Uściśla rozwój danej konstrukcji, wyznaczając granice dla prac projektowych. Pozwala uniknąć ryzyka błędów inżynieryjnych dzięki wczesnej weryfikacji nietypowych i próbnych rozwiązań, mogących niekorzystnie wpływać na produkt na jakimkolwiek dalszym etapie prowadzenia procesu projektowego.
W efekcie skracamy czas prowadzenia projektu. Dysponując konkretnymi wynikami symulacji, oceniamy jakość naszej konstrukcji i eliminujemy niespodziewane błędy związane z eksploatacją produktu, często niedostrzegalne w pierwszych etapach prac. To wszystko przekłada się na odczuwalne przez organizację przyspieszenie procesów projektowych i podniesienie jakości i innowacyjności produktów.

Znaczenie odpowiednich narzędzi
Odwrócenie paradygmatu i zmiana przyzwyczajeń w procesie badawczo-rozwojowym niesie ze sobą też konkretne wymagania w stosunku do przedsiębiorstw przemysłowych. Tylko odpowiednie narzędzia, które doskonale wymieniają się danymi, umożliwiają rzeczywiste zwiększenie efektywności poprzez eliminację niepotrzebnych powtórek badawczych. Uwagi wymaga również dostępność narzędzi analityczno-symulacyjnych. Ograniczona liczba specjalistów dokonujących symulacji stanowi dzisiaj jedną z podstawowych barier na drodze do optymalizacji procesu projektowego. Zmiana w tym zakresie wymaga implementacji narzędzi, które funkcjonują w jednym środowisku, mają niską barierę wejścia i są równie łatwe w opanowaniu dla konstruktora, jak również specjalisty z zakresu symulacji i analiz.
Narzędzia spełniające takie kryteria, a jednocześnie dające dostęp do wystarczająco dużego zakresu informacji, mogą znacząco skrócić czas procesu projektowego. Wykonanie symulacji jest możliwe w oparciu o model wstępny, czyli nawet w sytuacji, kiedy nie mamy pełnej dokumentacji czy modelu 3D. To przekłada się na zauważalne przyspieszenie prac i ułatwia opracowanie projektów zgodnych z wymaganiami taktyczno-technicznymi.
"Shift-left" (przesuń na początek) trendem zauważanym przez polski sektor obronny
Proces wprowadzania produktu na rynek w przypadku przemysłu obronnego składa się z kilku zmiennych, które działające w tym sektorze organizacje nieustannie biorą pod uwagę. Wynikowy czas i koszt zmiany jest tym wyższy, im później do niej dochodzi. Z upływem czasu projektu maleje przestrzeń do wprowadzania zmian konstrukcyjnych, a także rośnie złożoność napraw wszelkich wykrytych błędów i problemów. Z tego względu na całym świecie obserwuje się obecnie trend "shift-left" (przesuń na początek), w którym przedsiębiorstwa starają się jak najwięcej działań podejmować na wczesnym etapie procesu inżynieryjnego, kiedy możliwości zmian są największe, modyfikacje najmniej skomplikowane a projekt można poddawać nawet gruntownym przebudowom.
Inwestycja w narzędzia z zakresu Product Design & Engineering, którego częścią łatwą do zaimplementowania w innych środowiskach jest portfolio rozwiązań do analiz symulacji i testów, stanowi kluczowy aspekt na coraz bardziej konkurencyjnym rynku przemysłu obronnego. To szansa będąca dziś na wyciągnięcie ręki dla polskiego sektora, z której zdecydowanie warto skorzystać.
Artykuł sponsorowany, partner publikacji Siemens Digital Industries Software
WIDEO: Święto Wojska Polskiego 2025. Defilada w Warszawie