Jak cyfrowy bliźniak praktycznie zmienia sposób działania firm przemysłowych
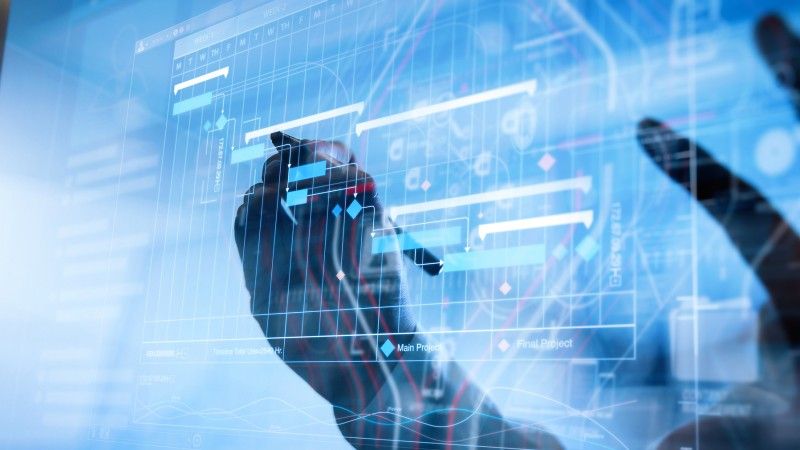
W dzisiejszym dynamicznym i konkurencyjnym środowisku przemysłowym, firmy coraz bardziej polegają na nowych technologiach. To dzięki nim osiągają przewagę konkurencyjną i mogą sprawnie odpowiadać na potrzeby rynku. Do grona najbardziej innowacyjnych i obiecujących rozwiązań należy cyfrowy bliźniak. Potencjał technologii potwierdzają przykłady wdrożeń w przedsiębiorstwach, które nawiązały bliską współpracę z Siemens Digital Industries Software.
Artykuł sponsorowany, partner publikacji Siemens Digital Industries Software
Cyfrowy bliźniak łączy dane z sensorów, systemów analitycznych oraz modeli symulacyjnych, by umożliwiać monitorowanie, analizę i optymalizację w czasie rzeczywistym. Jako wirtualny odpowiednik rzeczywistego obiektu znajduje zastosowania w trzech głównych obszarach przemysłu - projektowaniu i rozwoju produktu, optymalizacji procesów produkcyjnych oraz monitorowaniu i utrzymaniu. W każdym z nich oferuje unikalne możliwości i korzyści, przyczyniając się do poprawy efektywności, oszczędności czasu i zasobów, oraz zwiększania jakości i niezawodności.
Czytaj też
Potwierdzają to organizacje działające w sektorach obronnym i przemysłowym, które postawiły na cyfrową transformację i nowoczesne narzędzia w ramach modernizacji infrastruktury i usprawniania wewnętrznych procesów.
Praktyczny wymiar cyfrowego bliźniaka produktu
Cyfrowy bliźniak produktu zawiera szczegółowe informacje o strukturze, komponentach i zachowaniu produktu. Tworzony na etapie rozwoju i wykorzystywany przez cały cykl życia, pozwala na symulację i analizę zachowań w różnych sytuacjach oraz monitorowanie wydajności i wymagań konserwacyjnych. W ten sposób pomaga w optymalizacji projektu, identyfikacji potencjalnych problemów na wczesnym etapie oraz poprawie funkcjonalności i niezawodności produktu.
Technologia staje się coraz częściej podstawą funkcjonowania zespołów inżynierskich, które otrzymują nową przestrzeń do współdziałania i płynnej wymiany informacji w środowisku projektowym. Przekłada się to na większą innowacyjność, ogranicza występujące błędy i skraca czas potrzebny na dostarczenie produktu na rynek.
Czytaj też
- Projektowanie cyfrowe od SiemensaSponsorowany
Z tych możliwości korzysta dzisiaj między innymi koncern Airbus, który zaadaptował w funkcjonującym środowisku Lean PLM oprogramowanie z portfolio Xcelerator firmy Siemens Digital Industries Software oraz cyfrowego bliźniaka systemów elektrycznych i elektronicznych w całym cyklu rozwoju, produkcji i eksploatacji. Utworzone zunifikowane środowisko projektowe przyspiesza rozwój produktu, optymalizuje produkcję systemów elektrycznych i zauważalnie wpływa na czas, w którym uzyskiwane są wiązki elektryczne wyższej jakości. Zmiany w procesie prowadzą do wzrostu produktywności i przyspieszają rozwój komercyjnych samolotów producenta.

Zaawansowane rozwiązania programowe wykorzystuje też na co dzień zespół inżynierów ADG Mobility, firmy z sektora obronnego, która projektuje między innymi pojazdy opancerzone. Dzięki bliskiej współpracy z Siemens Digital Industries Software przedsiębiorstwo wprowadziło usprawnienia w procesach projektowania i wdrożyło narzędzia symulacyjne oraz system PLM umożliwiający zarządzanie danymi produktu i procesami rozwoju.
Pełna integracja z modelem CAD zapewniła konstruktorom możliwość wprowadzania wyników przeprowadzanych analiz do procesu projektowania bez konieczności ich eksportowania i mogącej powodować błędy oraz opóźnienia ręcznej aktualizacji. ADG Mobility wykorzystuje dziś symulacje, by ograniczać liczbę fizycznych prototypów – eksperci mogą w wirtualnej rzeczywistości monitorować wydajność ruchu, struktury czy też przepływ płynów. To wszystko umożliwia lepsze zarządzanie konfiguracjami, zmianami projektowymi i procedurami zatwierdzania, a tym samym pozwala sprawniej odpowiadać na potrzeby klientów w zakresie coraz bardziej złożonych produktów.
Czytaj też
Cyfrowy bliźniak produkcji w praktyce
Cyfrowy bliźniak produkcji koncentruje się na wirtualnej reprezentacji procesu produkcyjnego. Odzwierciedla fizyczny system produkcyjny, wszystkie maszyny, sprzęt i wykorzystywane zasoby oraz procesy. Na tej bazie przedsiębiorstwa mogą symulować, monitorować i optymalizować różne aspekty procesu.
Dzięki dostępnym rozwiązaniom technologicznym, kolejne organizacje mogą identyfikować wąskie gardła, optymalizować sekwencje produkcyjne i poprawiać alokację zasobów. Analizując i symulując różne scenariusze, podejmują bardziej świadome decyzje w celu zwiększenia wydajności, produktywności i elastyczności produkcji.
Jak to wygląda w praktyce, pokazuje firma GKN Aerospace, która wdrożyła rozwiązanie Plant Simulation z portfolio Xcelerator firmy Siemens Digital Industries Software. Wykorzystanie dynamicznego środowiska 3D i danych pozwoliło na lepsze zrozumienie procesu produkcyjnego i wykorzystania zasobów. Organizacja zaadaptowała również diagram Sankeya do reprezentacji ruchu materiałów i zatrudnionych specjalistów, co pomogło precyzyjnie zobrazować złożoność i współzależności w produkcji.
Czytaj też
Za sprawą Plant Simulation GKN Aerospace znalazła sposób na lepsze wykorzystanie zbieranych ogromnych ilości danych, których wcześniej nie umiała spożytkować w pełni. To z kolei przełożyło się na doskonalenie procesów i pozwoliło odpowiedzieć na wyzwania związane z planowaniem produkcji i oczekiwaniami klientów w zakresie dostaw. Firma zweryfikowała między innymi przewidywania dotyczące wąskich gardeł i znalazła obszary, w których optymalizacja procesów przyniesie największe korzyści.
Technologia dostępna na wyciągnięcie ręki
Inwestycja w nową linię produkcyjną czy maszyny do postawienia w fabryce wydaje się naturalnym sposobem na dalszy rozwój firmy. W dobie szybko postępującej cyfryzacji sektor obronny nie może jednak ignorować innej ścieżki, która przynosi szybko zauważalne korzyści. Raporty potwierdzają, że wykorzystanie potencjału kompleksowego cyfrowego bliźniaka i algorytmów sztucznej inteligencji w ramach cyfrowej inżynierii produktu pozwala na skrócenie czasu wprowadzenia produktu na rynek nawet o 40%.
Te możliwości są dzisiaj dostępne na wyciągnięcie ręki dla firm z sektora obronnego. Z pomocą zaufanych partnerów, jak Siemens Digital Industries Software, rozwiązania cyfrowe mogą być efektywnie wdrażane i stosowane w praktyce. To fundament, na którym cały polski sektor może dziś budować swoją pozycję, zbliżając się do czołówki światowego rynku.
Artykuł sponsorowany, partner publikacji Siemens Digital Industries Software
WIDEO: Święto Wojska Polskiego 2025. Defilada w Warszawie