Przemysł Zbrojeniowy
Większe tempo produkcji Hawkeia
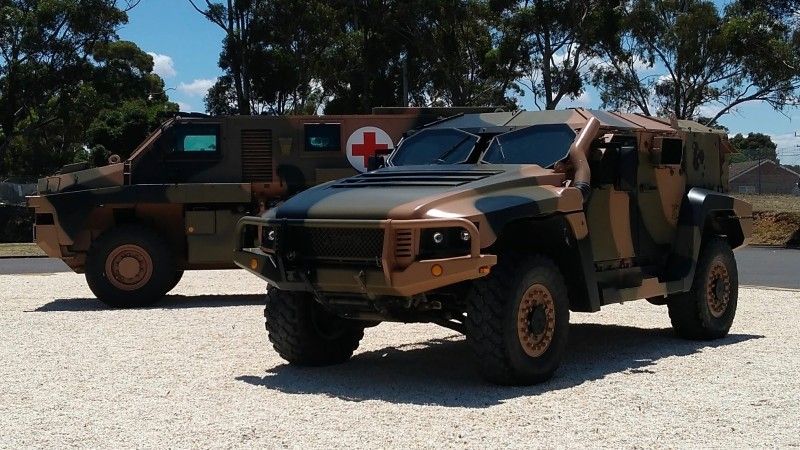
Pod koniec kwietnia br. Thales Australia poinformował o podwojeniu produkcji pojazdów Hawkei PMV-L (Protected Mobility Vehicle – Light) w fabryce w Bendigo. Ma to nie tylko przyspieszyć realizacje dostaw tych wozów, ale jest również istotne z punktu widzenia wsparcia dla kooperantów Thales i utrzymania stabilności łańcucha dostaw.
Fabryka w Bendigo, w stanie Wiktoria, jest głównym ośrodkiem Thales Australia w zakresie produkcji pojazdów opancerzonych. Miasto to, założone w połowie XVIII w. w okresie australijskiej gorączki złota, położenie jest ok. 150 km na północ od Melbourne. W 1941 roku zaczęła tu działać fabryka, w której początkowo produkowano armaty morskie różnych kalibrów. W późniejszym okresie uruchomiono również produkcję innych systemów artyleryjskich, w tym: 40 mm armat przeciwlotniczych Boforsa, 87,6 mm dział samobieżnych Yeramba, 120 mm dział bezodrzutowych BAT i 105 mm haubic L119.
W roku 2003 r. w zakładach, należących wówczas do Australian Defence Industries Ltd. (ADI) - jednego z głównych dostawców dla australijskiego Departamentu Obrony, uruchomiona została produkcja pojazdów opancerzonych Bushmaster IMV (Infantry Mobility Vehicle). W 2006 r. Thales, za zgodą australijskiego rządu, przejął pełną kontrolę nad ADI, co dało początek działalności Thales Australia.
Czytaj też: Holendrzy zamawiają minoodporne Bushmastery
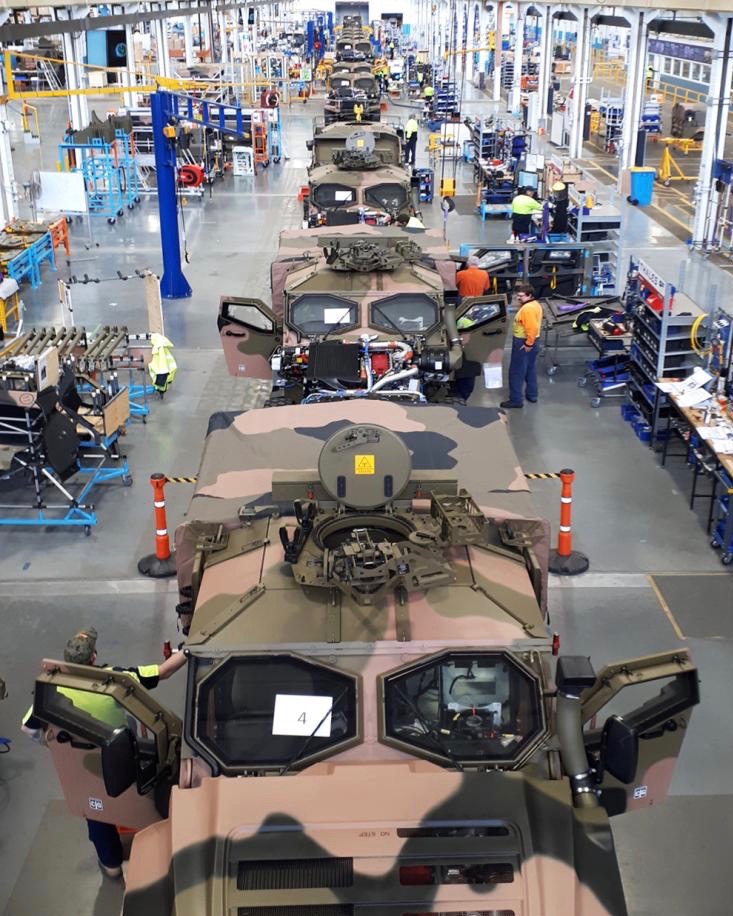
Obecnie zakład zajmuje obszar 37 hektarów, na którym znajdują się m.in. trzy hale przeznaczone do produkcji pojazdów. Poza nimi zlokalizowane są tu również biura konstrukcyjne oraz działy odpowiedzialne za organizacje i zarządzanie produkcją. W zakładzie wykonywane są również remonty oraz modernizacje i modyfikacje Bushmasterów eksploatowanych przez ADF. Poza Bendigo zaangażowane są jeszcze cztery inne, mniejsze ośrodki: Brisbane, Melbourne, Sydney i Townsville, zatrudniające w sumie ok. 450 pracowników.
W przypadku produkcji Hawkeia, którego kabina-cytadela jest dziełem izraelskiej firmy Plasan i wykorzystano w niej opatentowaną technologię Kitted Hull, do fabryki w Bendigo elementy kabiny dostarczane są w skrzyniach (każda kabina to jedna „paczka”), a na miejscu odbywa się ich składanie i pełna kompletacja.
Do kabiny-kapsuły, z przodu i z tyłu, przymocowane są pomocnicze ramy rurowe, do których z kolei zamocowane są elementy zawieszenia i układu napędowego pojazdu. Produkowane są trzy wersje ram: przednia i dwie tylne (dla 4- oraz 2-drzwiowej odmiany), a ich wykonanie to wieloetapowy proces. Każda rama jest spawana po kolei na kilkunastu stanowiskach, między którymi przemieszcza się na specjalnej kolumnie z kontrolowanym komputerowo obrotowym wysięgnikiem na którym jest zamontowana.
Każdy spawacz wykonuje dokładnie określoną ilość spawów w różnych miejscach ramy, co ma na celu zarówno zapewnić wysoką jakość połączeń, jak i utrzymać kontrolę nad temperaturą spawanych elementów ‒ nie może dojść do ich przegrzania. Jest to bardzo istotny proces z punktu widzenia wytrzymałości całej konstrukcji pojazdu, stąd spawacze pracujący w Bendigo to wysoko wykwalifikowani i doświadczeni pracownicy, którzy wcześniej odpowiedzialni byli za spawanie kadłubów Bushmasterów.
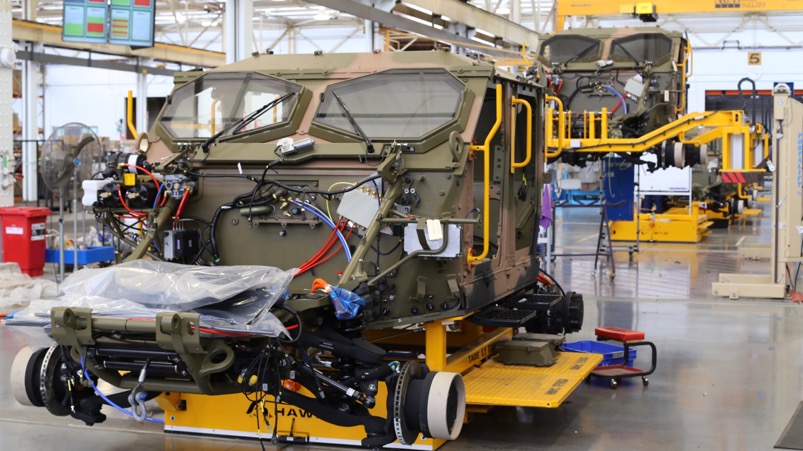
Wyspawane ramy są łączone ze skompletowanymi kabinami na linii produkcyjnej, której organizacja praca przypomina tę stosowaną w przemyśle motoryzacyjnym. Na kolejnych etapach, pomiędzy którymi przesuwa się kompletowany pojazd na specjalnym (projekt własny Thales Australia) transporterze, montowane są poszczególne podzespoły.
Całość procesu produkcyjnego zarządzana i kontrolowana jest na bieżąco, co możliwe jest dzięki wykorzystaniu odpowiednich narzędzi teleinformatycznych. Każdy pojazd otrzymuje swój indywidualny, elektroniczny „paszport”, co pozwala m.in. na weryfikację, czy ewentualna usterka lub wada, która się w nim pojawiła w trakcie eksploatacji może być związana z błędami popełnionymi w trakcie jego produkcji.
Czytaj też: Singapur i Australia rozbudują wspólnie poligony
Pod koniec 2016 roku w zakładach w Bendigo rozpoczęła się pilotażowa produkcja (low rate production) 100 pojazdów Hawkei PMV-L (Protected Mobility Vehicle - Light). Zgodnie z planami w połowie 2018 roku miała ruszyć pełnoskalowa produkcja (full rate production) o wydajności dwóch wozów dziennie (ok. 400 rocznie), co miało umożliwić dostawę do 2022 r. 1100 pojazdów.
Jednak w 2017 r. w wyników zbyt wysokiej awaryjności testowanych pojazdów doszło do opóźnienia programu. W sierpniu 2017 roku podpisano aneks do umowy, który zakładał powtórzenie testów. Zmieniono wówczas także harmonogram zakończenia produkcji pilotażowej na styczeń 2019 roku i seryjnej na czerwiec 2021 roku.
Polak z Polski
To jest pojazd, który nam jest potrzebny a nie jakieś Nissany.
fcuk
Za drogi. Około 2mln za sztuke. Z drugiej strony MON kupuje rosomaki do transportu 4 żołnierzy i 2 spików....
THXXX
I tak to powinno wyglądać w Rosomak S.A. Po zakończeniu produkcji Rosomaka czas na opancerzone 4x4 oraz 6x6 w ilości 1 sztuka dziennie (200 rocznie) plus remont/modernizacja Rosomaka w ilości 1 sztuka dziennie. Tylko taka organizacja daje szanse na efektywne wykorzystanie pieniędzy podatników i z korzyścią dla Armii.
Fanklub Daviena
"czas na opancerzone 4x4 oraz 6x6" - a komu wtedy Wielki Wuj sprzedawałby swoje chałowate Humvee? Dlatego zapomnij o tym... :)
fcuk
Moglibyśmy bez problemu dogadać się z SISU, na produkcję GPV. No ale skoro Estonii i Litwie wielki brat nie pozwolił, a kazał kupić JLTV, to nam też nie pozwoli.
Ruski funboy
Nie no. Humvee złe ale Tigr dobry. Su najlepsze, no i nie zapominam też, że najlepszym lotniskowcem jest kuznietsow
Kangorek
Koledzy z dawnej fabryki toyota pomagaja przy produkcji Widac wyraźnie BRAK dofinansowania linni montażowej, brak aitomatyki STĄD też awaryjność Trzymam kciuki
korsarz
roboty przy takiej wielkosci serii sa nieoplacalne
fcuk
Jaka automatyka przy 2000 sztuk?